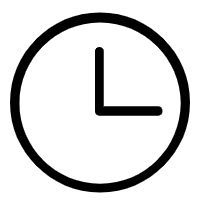
CNC lathe as an important processing equipment in modern manufacturing industry, its processing accuracy directly affects the quality of products and production efficiency. However, in the actual operation process, the accuracy may be unstable, which not only reduces the processing quality, but also may increase the scrap rate and affect the production schedule. The following are some common causes and analysis of the instability of CNC lathe accuracy:
1. Mechanical parts are worn or loose
After CNC lathes run for a long time, mechanical parts such as guide rails, lead screws, bearings, etc., are prone to wear, resulting in reduced positioning accuracy. At the same time, the loosening of the connector will also cause the vibration of the machine tool to intensify, further affecting the processing accuracy. Regular inspection and replacement of worn parts and tightening of loose screws are key to maintaining stable accuracy.
2. Control system error
Software or hardware failures of the CNC system, such as encoder errors, control board failures or improper system parameter Settings, can lead to inaccurate execution of machining instructions, which in turn affects the dimensional accuracy and surface roughness of the workpiece. Regular system diagnosis and calibration, update control software, and ensure that system parameters match the actual state of the machine are necessary maintenance measures.
3. Servo system does not respond in time
The performance of servo motor and drive system directly affects the dynamic response speed and accuracy of machine tool. If the servo system is improperly adjusted, the feedback delay or the response speed is slow, the following error will be increased during the machining process. Check the operating status of the servo system and adjust the gain parameters to ensure that it responds quickly and accurately to the control signal.
4. Tool wear or improper selection
The wear condition of the tool, the sharpness of the cutting edge and whether the selection is suitable will directly affect the machining accuracy. The worn tool will lead to uneven cutting force distribution and unstable cutting size; The unsuitable tool may not achieve the desired machining effect. Regular inspection of tool status and selection of appropriate tool materials and geometric parameters are essential for maintaining machining accuracy.
5. Environmental factors
Environmental factors such as temperature change, humidity, vibration will also affect the accuracy of CNC lathes. For example, temperature fluctuations can cause thermal deformation of the machine tool, affecting the positioning accuracy. The establishment of a constant temperature workshop and the use of anti-vibration pads to reduce external vibration interference are effective methods to improve the impact of environmental factors.
6. Programming errors
Improper machining procedures or parameter Settings (such as unreasonable feed speed and cutting depth Settings) may also lead to machining accuracy problems. Optimize the programming strategy, ensure that the program logic is correct, and set the processing parameters reasonably according to the material characteristics and processing requirements.
In short, the reasons for the instability of CNC lathe accuracy are complex and diverse, and it is necessary to comprehensively consider many aspects such as mechanical, electrical, control software, tool selection, environmental conditions and programming, and take corresponding preventive and corrective measures to ensure continuous and stable processing accuracy and production efficiency. Regular maintenance, accurate debugging and good operating habits are important guarantees to improve the machining accuracy of CNC lathes.