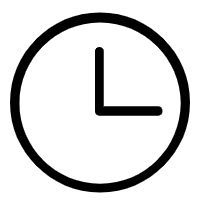
The commonly used tool setting methods in CNC machining centers mainly include the following:
1. Trial cutting tool setting method: This is a simple and convenient method, but it will leave cutting marks on the surface of the workpiece and the tool setting accuracy is low. The trial cutting tool setting method usually takes the tool setting point (which coincides with the origin of the workpiece coordinate system) at the center of the workpiece surface as an example, and adopts a bilateral tool setting method.
2. Tool setting method with tool setter: This is a more accurate and commonly used tool setting method. Tool setters are divided into two types: in-machine tool setters and external tool setters. Tool setting with an external tool setter needs to be calibrated outside the machine tool in advance, and then the tool can be installed on the machine tool. Tool setting with an on-machine tool setter is a method of directly installing the tool at a fixed position on the machine tool for measurement. .
3. Automatic tool setting method: This is accomplished by using the tool detection function of the CNC machining center. It can automatically and accurately measure the length of each tool in each coordinate direction, and can automatically correct the tool error value. The entire detection and correction process can be completed based on the normal operation of the machine tool, eliminating human errors in tool setting, so the tool setting accuracy is higher and the tool setting efficiency is also better.
In addition, there are tool setting methods such as edge finders, eccentric rods and axis setters, which are also a commonly used tool setting method. The specific operation steps are similar to the trial cutting tool setting method, except that the tool is replaced with an edge finder or eccentric rod. When using the edge finder, care must be taken to ensure that the steel ball part is in slight contact with the workpiece. At the same time, the workpiece to be processed must be a good conductor and the positioning reference surface must have good surface roughness.
Each of these methods has its own characteristics, and which method to use depends on factors such as the specific requirements of the workpiece, the configuration of the machining center, and the proficiency of the operator. In practical applications, the most appropriate tool setting method can be selected according to the specific situation.