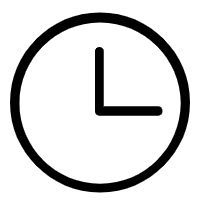
The spindle taper hole of the machining center is an important component that connects the spindle and the tool. It is responsible for transmitting the rotational force and momentum of the spindle and withstanding the cutting load and large inertial load during the machining process. Therefore, when choosing a machining center, it is very important to understand the type, structure and performance indicators of the spindle taper hole, which will help improve processing efficiency and quality, and reduce equipment failure rate and maintenance costs.
The main types of spindle taper holes include BT, CAT, HSK, ISO, SK, etc. Among them, BT and CAT are the more commonly used standard models, while HSK and ISO are more suitable for high-speed and high-precision processing. SK is a European model, similar to CAT and BT, but its spindle taper hole wall is thinner, which can improve the spindle load-bearing capacity and rigidity. According to actual needs and equipment requirements, choosing different types of spindle taper holes can achieve the best processing results.
There are also differences in the structure of the spindle taper hole. The common ones are single taper hole and multi-taper hole. The single-taper hole has a simple structure and is easy to process and install, but its load-bearing capacity and rigidity are slightly inferior to those of multi-taper holes. The multi-taper hole structure can improve the load-bearing capacity and rigidity of the spindle, making processing more stable and accurate. In addition, some spindle taper holes have cooling systems that can circulate coolant to the tool and processing area during processing, effectively reducing the processing temperature and improving processing quality.
The performance indicators of the spindle taper hole mainly include load-bearing capacity, rigidity, accuracy and dynamic balance. The load-bearing capacity refers to the maximum load-bearing capacity of the spindle taper hole under load. Generally, the bigger the better. Rigidity refers to the degree of vibration and deformation of the spindle taper hole during machining, which has a significant impact on machining accuracy and surface quality. Accuracy refers to the influence of the geometry and factors of the spindle taper hole on the accuracy of the machining results. Generally, the requirements are as high as possible. Dynamic balance refers to the balance performance of the spindle taper hole during high-speed rotation, which has a greater impact on machining accuracy and tool life.
In short, understanding the type, structure and performance indicators of the spindle taper hole can help select appropriate machining center equipment, improve production efficiency and quality, and prevent economic losses caused by equipment failure. As an important part of the manufacturing industry, the technology of spindle taper holes is constantly updated and innovated, and there will definitely be more development space and application fields in the future.