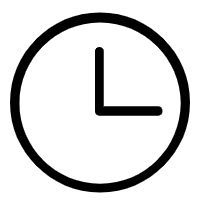
Precision CNC lathes need to avoid various errors during processing to ensure the quality of the final product. Here are some common types of errors and how to avoid them:
1. Geometric error:
Reasons: CNC lathe structure, guide rail wear, transmission system problems, etc.
Methods to avoid: Carry out regular machine tool maintenance on CNC lathes, check and adjust the geometric structure of the machine tool, and ensure the geometric accuracy of the machine tool.
2. Thermal error:
Reason: Long-term operation of CNC lathes causes the temperature of machine tool parts or workpieces to increase, causing dimensional changes.
Methods to avoid: Use temperature control equipment on CNC lathes, minimize machine tool operating time, and adopt a stable working environment.
3. Tool error:
Reason: CNC lathe tool wear, edge damage, edge cracking, etc.
How to avoid: Regularly replace worn tools on CNC lathes, ensure the geometry and edge quality of the tools, and use appropriate tool materials.
4. Clamping error:
Reason: The workpiece clamping of the CNC lathe is not firm and there is a problem with the clamp.
Methods to avoid: Check the fixation of the CNC lathe fixture to ensure that the workpiece is firmly clamped and use appropriate clamping methods to avoid deformation.
5. CNC program error:
Reason: CNC lathe CNC program error and parameter setting problem.
How to avoid: Carefully check and verify CNC lathe CNC programs to ensure their correctness. Adjust processing parameters according to material and process requirements.
6. Material error:
Reason: CNC lathe material hardness, uneven material, etc.
How to avoid it: Make sure you choose the right tool and cutting parameters for your CNC lathe to handle the characteristics of different materials. Check the quality of materials regularly.
7. Operation error:
Reason: CNC lathe operator lacks experience or skills.
Methods to avoid: CNC lathes provide training to ensure that operators are familiar with the operating procedures of CNC lathes and understand how to set and adjust processing parameters.
8.Measurement error:
Reason: Accuracy problem of CNC lathe measuring tools.
How to avoid it: CNC lathes use high-precision measuring tools and regularly calibrate and check measuring equipment.
Through regular maintenance, reasonable setting of processing parameters, selection of appropriate tool and workpiece clamping methods, and training of operators, errors in the precision CNC lathe processing process can be effectively avoided and the accuracy and stability of the product can be improved.