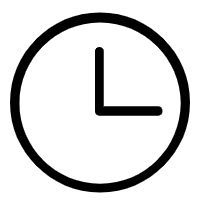
Several factors need to be considered when selecting and maintaining CNC machine tool equipment, including budget, processing needs, technical requirements, and equipment reliability and durability. Here are some suggestions for selecting and maintaining CNC machine equipment:
Select CNC machine tool equipment:
1. Processing requirements:
Determine your CNC machine tool processing needs, including material type, processing size, processing accuracy requirements, etc.
Choose the appropriate CNC machine tool type according to the CNC machine tool processing needs, such as lathes, milling machines, drilling machines, etc.
2..Technical requirements:
Consider your CNC machine operating skills and employee training needs. Some CNC machine tools may require a higher level of operating skills.
Consider the degree of automation and intelligence of CNC machine tool equipment to improve CNC machine tool production efficiency and reduce human operating errors.
3. Brand and quality:
Choose CNC machine tool manufacturers from well-known brands. They usually have more reliable products and better after-sales services.
Read user reviews and industry reputation to learn about the device's performance and reliability.
4. Budget and Cost:
Determine the appropriate CNC machine model and configuration based on your budget.
Consider the long-term operating costs of CNC machine tool equipment, including energy consumption, maintenance costs, etc.
5.Technical support and after-sales service:
Ensure that CNC machine tool manufacturers provide timely technical support and after-sales services, including training, maintenance, etc.
Maintenance of CNC machine tool equipment:
1. Regular maintenance:
Develop a regular CNC machine tool maintenance plan, including cleaning, lubrication, tightening and other operations.
Regularly check the degree of wear of various components of CNC machine tool equipment and replace worn parts in a timely manner.
2. Cleaning and Lubrication:
Regularly clean the exterior and interior of CNC machine tools to keep the equipment clean.
Regularly add lubricating oil to the CNC machine tool lubrication system to ensure that all components are well lubricated.
3. Check and adjust:
Regularly check the parameter settings and programs of the CNC machine tool CNC system to ensure its normal operation.
Check the mechanical components of CNC machine tool equipment, including transmission systems, guide rails, etc., and adjust and tighten loose components.
4. Training and operating specifications:
Provide training to CNC machine tool operators and teach them correct operating skills and maintenance methods.
Develop CNC machine tool operating specifications and standardize operating procedures to reduce equipment misoperation and damage.
5. Record and track:
Record the maintenance status and fault records of CNC machine tool equipment, and establish equipment files.
Develop more scientific maintenance plans and preventive measures based on recorded CNC machine tool data.
Through the above methods, you can select suitable CNC machine tool equipment, maintain its good operating condition, and improve production efficiency and product quality.