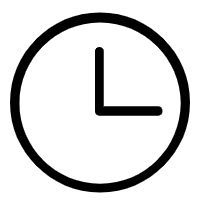
Ensuring the machining accuracy of a horizontal machining center is a comprehensive engineering challenge, which involves multiple aspects such as the design, maintenance, operation specifications, and optimization of the machining process of the machine tool itself. The following are some key strategies and steps that can help improve and maintain the machining accuracy of horizontal machining centers:
Firstly, optimization of the machine tool itself
1. Choose high-quality machine tools: In the procurement stage, it is crucial to choose a machine tool with high rigidity and precision. Machine tools should have good stability, effective vibration reduction measures, and precise servo drive systems.
2. Spindle design: The spindle adopts three-point support, with high-precision bearings used at the front and middle ends, such as a combination of short cone double row roller bearings and large contact angle ball bearings, and single row cylindrical roller bearings used at the rear end to ensure high rigidity and excellent rotation accuracy of the spindle.
3. Guide rail system: Adopting wide cast iron hardened precision grinding guide rails, reducing the phenomenon of low-speed crawling of the machine tool, improving positioning accuracy and dynamic response characteristics.
Secondly, tool selection and management
1. Tool selection: Reasonably select tools that are suitable for the material and shape being processed, avoid tool deformation during the processing, and ensure the sharpness and durability of the tools.
2. Tool clamping: Use a high-precision tool clamping system to ensure that the tool is firmly clamped on the spindle, reducing machining errors caused by tool looseness.
Thirdly, optimization of cutting parameters
1. Cutting parameters: Adjust the cutting speed, feed rate, and cutting depth based on material hardness, tool type, and machine performance to achieve the best machining effect and surface smoothness.
Fourth: Process flow control
1. Workpiece clamping: Use appropriate fixtures to ensure the stability and repeated positioning accuracy of the workpiece during the machining process.
2. Machining path planning: Optimize the machining path, reduce idle travel time, and avoid unnecessary changes in cutting force to maintain the smoothness of the machining process.
Fifth: Temperature control
1. Thermal stability: Control the working temperature of the machine tool to reduce the thermal expansion and contraction of machine tool components caused by temperature changes, which affects machining accuracy.
Through the comprehensive implementation of the above measures, the machining accuracy of the horizontal machining center can be significantly improved, and its long-term stable working performance can be maintained, thereby meeting the manufacturing needs of high-precision parts.