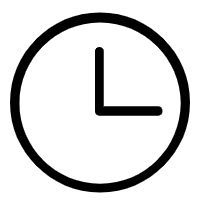
CNC vertical lathe is an efficient and precise machining equipment, which is widely used in high-precision mechanical parts, aerospace parts, automobile engines, turbines and other fields. However, when processing, the positioning of the workpiece is very important, because inaccurate positioning will cause the processed parts to not meet the requirements, seriously affecting the production process. So, how to find the workpiece positioning reference plane for CNC vertical lathe? The following is a detailed introduction for you.
1. Establish an initial reference surface
When processing a workpiece on a CNC vertical lathe, an initial reference surface must first be established on the workpiece. The initial reference surface is a flat, undamaged, bumpy or curved surface selected from the workpiece. The initial reference surface is the starting point for processing the part, so its flatness and verticality must be guaranteed.
2. Find the datum and zero point
Under normal circumstances, the CNC vertical lathe datum plane is usually the initial reference plane, and now we need to find it. The datum plane is the beginning of the zero point, which determines the starting point of the machined part and the datum of the entire machining process. To find the datum plane and zero point, precise measurements can be made with measuring tools, such as micrometers, height gauges, blank gauges, and other tools. By comparing the measured values, find a surface that can be used as a reference surface, and then mark or scale it as a reference for the next processing.
3. Determine the machine tool reference point
After the CNC vertical lathe determines the datum plane and zero point of the workpiece, we also need to determine the reference point of the machine tool and fix it first. The reference points of machine tools are mainly divided into two categories, one is the zero point and the other is the program starting point. The reference point of the machine tool is the starting point or end point of the processing program, so its accuracy must be guaranteed. Generally speaking, the selection of reference points for CNC vertical lathes is based on the processing technology and machine tool structure.
4. Carry out auxiliary positioning
After determining the datum plane, zero point and machine tool reference point, CNC vertical lathes also need to perform auxiliary positioning to ensure machining accuracy. Auxiliary positioning is generally achieved using positioning blocks. The positioning block is a relatively precise workpiece with accurate dimensions and high surface smoothness. Install the positioning block on the datum surface and adjust it so that it coincides with the machine tool reference point, and then perform frequent inspections. If the exact position of the positioning block is determined, processing can be carried out.
5. Check the processing accuracy
Finally, the machining accuracy needs to be checked at all times when performing the machining process. During the processing process, it is necessary to continuously fine-tune processing parameters, such as tool depth, speed, feed, etc., to ensure processing accuracy. If problems are found during processing, stop processing in time and make necessary adjustments to ensure the stability of processing accuracy.
To sum up, finding the workpiece positioning reference plane of a CNC vertical lathe is a key part of the processing process, and its accuracy has an important impact on the yield and processing efficiency of processed parts. Therefore, during the processing process, the above steps must be strictly followed, and the processing accuracy must be strictly checked. Only in this way can high-quality parts be produced and production efficiency improved.