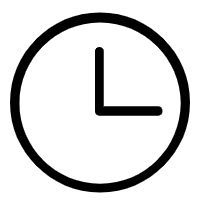
Improving the working efficiency of small vertical lathes is a comprehensive task that involves optimization and improvement in many aspects. Here are some key strategies and approaches:
Optimize the structural design of machine tools: The structural design of small vertical lathes has a direct impact on their work efficiency. By optimizing the structural design, the vibration and friction of the small vertical lathe during the processing can be reduced, the stability and accuracy of the machine tool can be improved, and the work efficiency can be improved.
Reasonable selection of cutting tools: The selection of cutting tools for small vertical lathes is crucial to processing efficiency and quality. Appropriate tool materials and angles should be selected based on factors such as processing materials and processing methods. At the same time, regularly check and replace severely worn tools to ensure that the tools are in optimal working condition.
Optimize the process plan: Develop a reasonable process plan for small vertical lathes, including processing sequence, cutting parameters, etc., which can reduce the empty stroke and non-processing time during the processing and improve processing efficiency. In addition, by adopting composite processing methods, such as turning and milling combined processing, boring and milling processing, etc., the process flow can be further simplified and production efficiency improved.
Use CNC system: Small vertical lathe CNC system can achieve precise control of the machine tool and improve processing accuracy and efficiency. By writing programs and inputting instructions, each motion axis of the machine tool can be controlled to achieve automated processing. At the same time, the CNC system can also monitor the processing process in real time and automatically adjust cutting parameters to achieve optimal processing results.
Strengthen equipment maintenance and upkeep: Carry out regular maintenance and upkeep on small vertical lathes to ensure that they are in good working condition. This includes cleaning machine tools, checking lubrication systems, tightening loose parts, etc. Through maintenance, the failure rate of small vertical lathes can be reduced, the service life can be extended, and work efficiency can be improved.
Improve the skill level of operators: The skill level of operators also has a great impact on the working efficiency of machine tools. Through training and practice, the skill level of operators can be improved so that they can master the operation and programming skills of machine tools, reduce operating errors and failure rates, and improve processing efficiency.
To sum up, improving the work efficiency of small vertical lathes requires starting from many aspects, including optimizing machine tool structural design, rationally selecting cutting tools, optimizing process plans, using CNC systems, strengthening equipment maintenance and upkeep, and improving operator skill levels, etc. . By comprehensively applying these strategies and methods, the work efficiency of small vertical lathes can be significantly improved and greater economic benefits can be created for the enterprise.