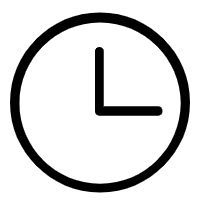
To process high-quality parts on a CNC vertical lathe, you need to pay attention to a series of factors, including machine tool performance, tool selection, cutting parameters, workpiece fixation, etc. Here are some suggestions:
1. Machine tool selection and adjustment:
CNC vertical lathes choose high-precision and high-rigidity CNC vertical lathes to ensure the stability and accuracy of the machine tool itself.
Ensure the adjustment and calibration of each axis of the CNC vertical lathe to ensure the movement accuracy of each axis.
2. Tool selection and installation:
CNC vertical lathe selects high-quality tools that suit the material and processing requirements.
Ensure the correct installation of CNC vertical turning tools, including tool holder clamping and tool alignment.
3. Cutting parameter settings:
CNC vertical lathe determines appropriate cutting speed, feed rate and depth of cut. This requires consideration of factors such as material hardness, tool materials and coatings, workpiece geometry, and more.
Use appropriate tool paths and tool compensation for CNC vertical lathes to minimize changes in cutting force.
4. Cooling and lubrication:
CNC vertical lathe ensures that the tool and workpiece receive sufficient cooling and lubrication during processing to prevent overheating and extend tool life.
Ensure the fluidity and cleanliness of CNC vertical lathe coolant to prevent impurities in the cutting fluid from damaging the tool and workpiece surface.
5. Workpiece fixation:
Choose an appropriate clamping device for the CNC vertical lathe to ensure that the workpiece remains stable during processing.
To avoid vibration and deformation of CNC vertical lathe workpieces, use appropriate support and clamping methods.
6. Precision processing technology:
CNC vertical lathes use advanced CNC programming technology, including high-speed cutting, dynamic compensation and other functions to improve machining accuracy.
CNC vertical lathes adopt advanced surface processing strategies to reduce surface roughness and improve surface quality.
7. Quality inspection and control:
CNC vertical lathes implement quality control measures, including regular tool testing, machine tool accuracy testing and workpiece dimensional measurement.
CNC vertical lathes can consider using automated testing equipment, such as laser measuring instruments, optical measuring instruments, etc., to improve the accuracy of testing.
8. Continuous improvement:
CNC vertical lathes continuously analyze problems in the processing process and make continuous improvements.
Utilize the data collection function of the CNC system to conduct real-time monitoring and optimization of the production process.
By comprehensively considering the above factors, the ability of CNC vertical lathes to process high-quality parts can be improved to meet high-precision and high-quality engineering requirements.