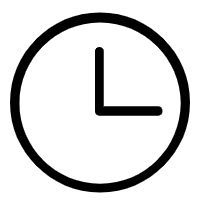
With the gradual development of CNC lathe technology, CNC machining has become an important processing method in industrial production, and CNC lathes, as important equipment in CNC machining, are widely used. However, during the use of CNC lathes, the problem of tool wear has always existed, which not only increases processing costs and affects product quality, but also causes damage to the lathe itself. Therefore, how to reduce the wear of CNC lathe tools has become one of the focus issues of CNC machining workers.
1. Reasonably select tool materials
The tool material of CNC lathe has a vital impact on tool life. If the material is improperly selected, the wear of the tool will be accelerated and the service life of the tool will be shortened. In order to solve this problem, we can choose cutting tools of different materials according to different processing materials. For example, for the processing of iron materials, we can choose wear-resistant materials such as high-speed steel and cemented carbide as tool materials, while for the processing of stainless steel, aluminum alloys and other materials, we can choose high-hardness cubic silicon nitride or cubic alumina. and other tool materials. The selection of tool materials must be careful, and based on comprehensive considerations such as processing materials, production batches, cutting parameters, cutting speed and other factors, try to select tool materials with better cutting performance.
2. Reasonably select tool geometric parameters
Tool geometric parameters also play a vital role in the tool life of CNC lathes. Reasonable selection of tool geometric parameters can effectively reduce cutting force and friction, thereby slowing down tool wear and extending tool life. If you choose a cutting tool with a smaller edge angle, you can reduce friction and heat accumulation, thereby extending tool life. In addition, choosing the appropriate profile and cutting angle can effectively reduce the friction on the tool surface, thereby reducing tool wear.
3. Reasonable selection of cutting parameters
Cutting parameters also play a non-negligible role in the tool life of CNC lathes. Reasonable selection of cutting parameters can help slow down tool wear while ensuring processing efficiency and product quality. In specific operations, attention should be paid to reasonably controlling parameters such as workpiece feed speed, cutting speed, and cutting depth to avoid excessive processing parameters that may lead to accelerated wear of the workpiece and tool.
4. Scientific and correct tool lubrication
Tool lubrication is also one of the important factors affecting tool life. The scientific and correct selection of tool lubricants can fully meet the lubrication and reduce heat during processing, reduce tool wear and workpiece surface quality problems, and help extend tool life. In addition, attention should also be paid to regular replacement of lathe oil and cutting fluid to avoid tool wear caused by jamming and deposits.
5. Education and training and virtuous cycle
Correct use and management can extend the service life of cutting tools, reduce production costs, and improve product quality and production efficiency. In the process of using CNC lathes, it is necessary to strengthen the technical training of employees, improve maintenance awareness, timely repair and maintenance of lathe equipment, and maintain the normal operation of the equipment. Then a good cycle is actually very important and necessary in terms of design, process, manufacturing, installation, maintenance, etc. to create a cycle of superior quality.
In short, the emergence of CNC lathe tool wear problems not only affects processing efficiency and product quality, but also increases production costs and causes unnecessary waste. Therefore, in actual operations, we must choose tools of different materials according to different processing materials, reasonably select tool geometric parameters, rationally select cutting parameters, and scientifically and correctly select tool lubricants. At the same time, we must strengthen technical training for employees and improve maintenance awareness. , only by establishing a good cycle can we effectively reduce the wear of CNC lathe tools and provide better services for the company's production and manufacturing.