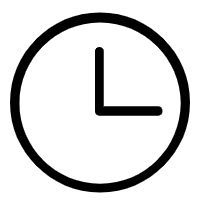
Turning tapers on a CNC lathe requires some special machining steps and parameter settings to be considered. Here are the general steps for turning a taper on a CNC lathe:
1. Preparation work: Before starting to turn the taper surface on the CNC lathe, ensure that the workpiece is firmly clamped, the workpiece and tool are in the correct position, and the machine tool parameters have been set.
2. Choose the right tool: For CNC lathes, choose a tool suitable for turning taper surfaces, usually using a tool with an inclined base tip. Make sure the knife is of good quality and has a sharp edge.
3. Determine the cutting direction: The CNC lathe determines the cutting direction of the cone surface and decides whether to turn from the big end to the small end or vice versa. In CNC programming, the movement direction of the tool relative to the workpiece needs to be properly set.
4. Set cutting parameters: In CNC programming for CNC lathes, set cutting parameters including cutting speed, feed speed, cutting depth, etc. The settings of these parameters need to be adjusted according to the workpiece material, tool type and processing requirements.
5. Set the coordinate system: In CNC programming for CNC lathes, ensure that the workpiece coordinate system and tool coordinate system are correctly set to ensure that the CNC system can accurately control the position of the tool.
6. Write CNC programs: CNC lathes write CNC programs, including initial point, cutting path, cutting depth and other information. Ensure that the program logic is correct to achieve precise machining of the cone surface.
7. Conduct trial cutting: Before formal processing on a CNC lathe, it is necessary to conduct trial cutting. Through trial cutting, you can check the accuracy of the program, determine whether the cutting parameters are appropriate, and adjust the required parameters.
8. Monitor the processing process: During actual processing, the CNC lathe continuously monitors the operation of the CNC lathe to ensure the stability of the tool and avoid vibration and other abnormal situations.
9. Regular measurement: CNC lathes regularly use measuring tools to check the size of the cone surface to ensure that the taper and accuracy of the processing meet the requirements.
10. Use of coolant: During the taper turning process of CNC lathes, coolant should be used rationally to reduce the cutting temperature and reduce the possibility of thermal deformation.
The above steps can help you smoothly turn the taper surface on the CNC lathe. Ensuring the accuracy of CNC programming and reasonably setting cutting parameters are the keys to achieving high-quality taper processing.