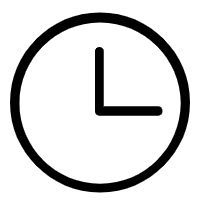
Lubrication and maintenance of CNC lathes are critical to maintaining machine tool accuracy, extending service life, and ensuring safe operation. The following is some knowledge about lubrication and maintenance:
Lubrication knowledge:
1. Select appropriate lubricating oil: Select appropriate lubricating oil according to different parts of the CNC lathe and the working environment, including machine tool guide rails, screws, bearings, etc.
2. Regular lubrication: Establish a CNC lathe lubrication plan and lubricate the machine tool regularly. The selection of lubrication cycle should take into account the frequency of use and environmental conditions of the machine tool.
3. Clean the working surface: Before lubricating the CNC lathe, make sure that the working surface, guide rails, etc. are clean. Avoid dust and debris from being mixed into the lubrication system to prevent damage to the machine tool.
4. Lubrication system automation: Some CNC machine tools are equipped with automatic lubrication systems, which can automatically complete lubrication tasks according to preset cycles and needs, improving the accuracy and efficiency of lubrication.
5. Moderate lubrication: Avoid excessive lubrication on CNC lathes. Excessive lubricating oil may cause carbon deposits, oil leakage and other problems. Control the amount of lubricant used according to the machine tool manual or manufacturer's recommendations.
Maintenance knowledge:
1. Regularly check all parts of the machine tool: CNC lathes regularly check all parts of the CNC lathe, including guide rails, screws, bearings, tool magazines, spindles, etc., to ensure that they are not abnormally worn or loose.
2. Pay attention to fastening bolts: Regularly check and tighten bolts on CNC lathes, especially the bolts connecting various parts of the machine tool. Make sure the machine tool structure is solid and will not loosen.
3. Clean the cooling system: CNC lathes clean the cooling system regularly to prevent chips and impurities from clogging the cooling pipes and maintain the normal circulation of cutting fluid.
4. Keep the environment clean: Keep the environment around the CNC lathe clean to prevent dust and debris from entering the machine tool and affecting the normal operation of the machine tool.
5. Regularly check the electrical system: Regularly check the electrical system of CNC lathes, including cables, terminal blocks, etc., to ensure that the electrical connections are good and to avoid problems caused by electrical faults.
6. Regularly replace consumable parts: CNC lathes need to regularly replace consumable parts on CNC lathes, such as cutting tools, tool sets, tool holders, etc. Arrange your replacement schedule appropriately based on usage and manufacturer recommendations.
7. Regularly calibrate the CNC system: CNC lathes regularly calibrate the CNC system to ensure the processing accuracy of the CNC lathe.
The above lubrication and maintenance knowledge should be combined with the specific CNC lathe model and usage conditions, and refer to the user manual and maintenance manual provided by the machine tool manufacturer to formulate a reasonable maintenance plan. Regular maintenance and upkeep will help keep your CNC lathe in good condition and ensure that it works efficiently and stably for a long time.