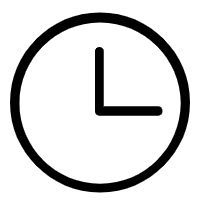
Horizontal machining centers, as high-end equipment in modern mechanical manufacturing industry, play an indispensable role in the mass production of complex parts with their high precision, high efficiency, and powerful processing capabilities. Among them, the spindle, as one of the core components of the machining center, its position and functional design are particularly crucial. In a horizontal machining center, the spindle is usually located in the vertical direction of the X-Y plane, that is, arranged along the Z-axis.
Design advantages of the spindle on the Z-axis
1. Optimization of spatial layout
The spindle of a horizontal machining center is installed perpendicular to the worktable, which allows the workpiece to be placed horizontally, providing stable support for large or heavy-duty workpieces and reducing deformation problems caused by self weight. Meanwhile, this design also facilitates the loading and unloading of workpieces and the use of fixtures, improving production efficiency.
2. Flexibility of Multi face Processing
The main spindle is arranged along the Z-axis, combined with a rotatable worktable (usually the fourth axis, i.e. the A-axis), which can achieve four-sided or five sided machining of the workpiece, without the need for re clamping to complete multi sided machining of complex parts, greatly improving machining accuracy and efficiency, and reducing clamping errors.
3. Tool proximity
The cutting tool of a horizontal machining center cuts from the top downwards, which is beneficial for the use of long cutting tools and particularly beneficial for the processing of complex cavities such as deep holes and cavities. The stability and rigidity of the cutting tool are enhanced, reducing vibration and ensuring machining quality.
4. Cooling and chip removal
The design of the spindle located on the Z-axis is also conducive to the effective supply of coolant and the smooth discharge of cutting chips. The coolant can be directly sprayed into the cutting area, effectively reducing cutting temperature and improving tool life; At the same time, due to the effect of gravity, the cutting chips naturally fall, reducing the friction between the tool and the cutting chips, and maintaining the cleanliness of the machining area.
Maintenance and technical challenges
Although the Z-axis spindle design of horizontal machining centers brings many advantages, it also comes with certain maintenance and technical challenges. For example, the high precision requirements of the spindle have raised higher standards for the selection, assembly, and maintenance of bearings; At the same time, managing the heat generated by long-term continuous processing and ensuring the stability of the spindle during high-speed operation are both technical challenges that require special attention.
In summary, designing the spindle on the Z-axis in a horizontal machining center is a clever layout based on improving machining efficiency, flexibility, and quality. It not only meets the needs of modern manufacturing for efficient and precision machining, but also provides an efficient solution for batch production of complex parts. With the continuous advancement of technology, horizontal machining centers and their spindle technology will continue to develop to meet more diverse machining needs.