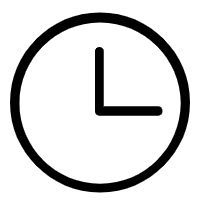
CNC lathe collisions can occur for a variety of reasons, some common ones include:
1. Programming error:
Incorrect G-code or M-code input can cause the tool to move in the wrong position, causing a collision. Programmers should carefully check and verify CNC programs to ensure their correctness.
2. Incorrect path planning:
Errors in tool path planning can cause the tool to move in inappropriate areas, colliding with the workpiece or fixture. Tool paths generated in CAM software should be carefully verified.
3. Workpiece clamping problem:
Improper workholding or fixture installation can cause the tool to collide with the workpiece. Make sure the fixture and workpiece are installed correctly and that the clamping force is appropriate.
4. Zero point and coordinate system errors:
If the zero point or coordinate system is set incorrectly, the CNC system will position the tool incorrectly. It is critical to correctly set up and verify the zero point and coordinate system.
5. Incorrect tool length and radius settings:
If the length or radius of the tool is set incorrectly, the CNC system may not be able to accurately calculate the actual position of the tool, resulting in a collision.
6. Machine tool mechanical problems:
Problems with the mechanical components of the machine tool, such as damaged guide rails, loose screws, etc., may lead to inaccurate tool positioning and collisions.
7. Tool wear or damage:
Using worn or damaged tools can lead to unstable cutting conditions and increase the risk of collisions.
8. Material changes:
During machining, the material properties of the workpiece may change, such as thermal deformation, which may cause tool-workpiece collision.
9. CNC system failure:
Hardware or software failures in the CNC system may cause incorrect instructions to be sent to the machine tool, causing a collision.
The key to preventing collisions lies in careful program writing and verification, correct tool path planning, and regular maintenance and inspection of machine tools and CNC systems. Using simulation software for program verification is also an effective way to reduce the risk of collisions.