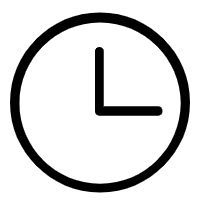
The vertical lathe needs to be tested before finalization to ensure its normal operation and efficient production. Before commissioning, it is necessary to conduct a comprehensive inspection of the lathe to see whether the components are assembled correctly, whether the parts are complete, whether the cleaning is in place, etc. Only through sufficient test runs and inspections can the normal operation of the lathe be guaranteed and lay the foundation for production work.
So, what problems may arise when testing a vertical lathe?
First, you need to pay attention to the electrical system of the lathe. Before commissioning, the electrical system needs to be inspected in detail to check whether the wiring is correct and whether there are short circuits and other problems to ensure the normal operation of the electrical system. At the same time, electrical components such as frequency converters and motors also need to be inspected to see if they are damaged or aged.
Secondly, the hydraulic system of the lathe needs to be checked. The hydraulic system is an important power system for lathes, and its normal operation has a vital impact on the quality and production efficiency of lathes. During the inspection, you need to check whether the oil level of the hydraulic system is normal, whether the cylinder is leaking or the one-way valve is damaged, etc., to ensure that the lathe hydraulic system is working properly.
Again, the lathe's lubrication system needs to be checked. Every part of the lathe needs lubricant to lubricate, and attention should be paid to each part requiring varying degrees of attention. Check whether the lubrication system is normal, whether the oil filling port is sealed, whether there are any pipeline blockages, etc., to ensure that all parts of the lathe can work smoothly.
Finally, the mechanical components of the lathe need to be inspected. The accuracy, fit, and gear matching of mechanical components all affect the accuracy and production efficiency of the lathe. The inspection points involve whether the gear box, bed guide rails are deformed, whether the spindle bearings, and the tool holder are operating normally, etc., to ensure the accuracy and quality of each component of the lathe.
The commissioning of vertical lathes requires careful and careful inspection and measurement. Only by ensuring the normal operation and efficient work of each component of the lathe can the production efficiency and work efficiency of the lathe be improved. Problems discovered during the lathe test run need to be recorded and resolved promptly to ensure efficient production of the lathe and create greater benefits for the enterprise.