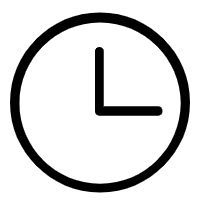
CNC lathe tool setting is one of the key steps to ensure processing quality and efficiency. The following are some commonly used CNC lathe tool setting methods and techniques:
1. Mechanical tool setting:
Mechanical tool setting is done by adjusting the relative position between the tool and the workpiece to maintain a certain distance, and then using manual operation or a fine-tuning device to adjust the position of the tool until the cutting tool contacts and aligns with the surface of the workpiece.
2. Inductive tool setting:
Inductive tool setting uses an inductor or sensor to detect the distance between the tool and the workpiece. When the tool approaches the workpiece surface, the CNC lathe sensor will send a signal indicating that the tool has been aligned with the workpiece surface.
3. Photoelectric tool setting:
Photoelectric tool setting uses equipment such as photoelectric sensors or laser rangefinders to detect the distance between the tool and the workpiece. When the tool approaches the workpiece surface, the CNC lathe will send out a signal indicating that the tool has been aligned with the workpiece surface.
4. Trial cutting and knife setting:
Trial cutting tool setting is to slightly contact the workpiece surface with the tool for trial cutting, and then the CNC lathe adjusts the position of the tool according to the cutting conditions after the trial cutting until the expected processing effect is achieved.
5. Zero point tool setting:
CNC lathe zero point tool setting is to set the zero point coordinates of the workpiece in the CNC system, move the tool to the zero point position, and then adjust the position of the tool to align it with the workpiece surface.
6. CNC system auxiliary function tool setting:
Many CNC lathes are equipped with automatic tool setting functions, which can be achieved through auxiliary functions in the CNC system, including automatic induction tool setting, automatic trial cutting tool setting, etc.
7. Notes:
During the tool setting process of a CNC lathe, attention should be paid to adjusting the position and direction of the tool to ensure uniform contact between the CNC lathe tool and the workpiece surface, and to avoid problems such as uneven cutting or excessively deep cutting.
Care must be taken during the tool setting process to avoid damaging the tool or workpiece and ensure safe production.
Regularly check and calibrate the tool setting function in the CNC system to ensure its accuracy and stability.
The above are the commonly used CNC lathe tool setting methods and techniques. Choosing the appropriate method and operating it correctly can improve processing efficiency and processing quality.