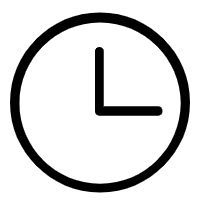
There are many reasons why CNC vertical lathes cause tool collisions, including but not limited to the following aspects:
1. Program writing errors: Errors in CNC vertical lathe process arrangements, poor consideration of process undertaking relationships, or incorrect parameter settings may lead to tool collisions. For example, the coordinates are set so that the bottom is zero, but in reality the top is 0; the safety height is too low, causing the tool to be unable to completely lift out the workpiece; after the program is written, the path of the program is not analyzed and checked, etc.
2. Program sheet remark error: CNC vertical lathe failed to adopt the principle of replacing old programs with new ones when changing program sheets, resulting in the old program sheets not being destroyed, causing confusion.
3. Tool measurement errors: For example, the tool setting data input of CNC vertical lathe does not consider the tool setting rod, the tool installation is too short, or the tool measurement does not use scientific methods or precise instruments.
4. The blank exceeds expectations: The blank of the CNC vertical lathe is too large and does not match the blank set by the program, resulting in tool collision.
Machine tool failure: CNC vertical lathes such as sudden power outages, lightning strikes, etc. may also cause tool collisions.
5. Improper operation: For example, the CNC vertical hand wheel is not skilled in the operation, and the tool collides with the workpiece; the safety height of the tool infeed and tool lift is not set enough, and collides with the fixture or workpiece boss; manual programming is improper, and the coordinates Value input or shape programming errors; when the CNC vertical lathe program is interrupted, the auxiliary function instructions are not re-called; manual temporary tool change errors, etc.
In order to reduce the occurrence of tool collision in CNC vertical lathes, operators need to be careful, operate the machine tool in the correct way, and perform regular maintenance and upkeep of the machine tool. At the same time, the use of anti-collision technology is also very important. For example, the development of advanced technologies such as CNC vertical lathe anti-collision detection systems and CNC vertical lathe adaptive processing can better protect CNC machine tools.
Please note that the above are just some common reasons, and the specific reasons may vary depending on equipment model, operation method, processing environment and other factors. In actual operations, we should pay close attention to the operating status of machine tools, discover and solve problems in time, and ensure the safety and efficiency of the processing process.