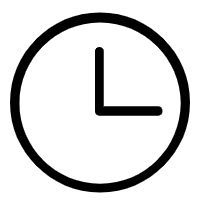
As a type of CNC lathe, CNC vertical lathe has high processing accuracy and efficiency and is widely used in the mechanical processing industry. However, in actual processing, we will find some problems, such as vibration marks on the outer diameter of the CNC vertical lathe, which will affect the processing quality and efficiency. So, what causes this situation?
First of all, vibration marks on the outer diameter of the CNC vertical lathe may be caused by uneven tool wear. During the machining process, tool wear is inevitable, and when the tool wear is uneven, chatter marks will appear. The solution to this problem is to regularly check and replace the cutting tools to ensure even wear of the cutting tools.
Secondly, the reason why the outer diameter of CNC vertical lathe has vibration marks may also be related to the workpiece material and its hardness. Some materials that are too hard or too fragile are prone to chatter marks during processing because it is difficult for the tool to achieve smooth cutting in these materials. The solution to this problem may be to change the machining process or use a tool more suitable for the workpiece.
In addition, the vibration marks on the outer diameter of the CNC vertical lathe may also be related to the CNC machining program. If the machining program is unreasonably written or contains errors, it is likely to cause chatter marks during machining. For this reason, the processing procedures need to be carefully checked and modified to ensure that the procedures are correct and effective.
Finally, vibration marks on the outer diameter of the CNC vertical lathe may also be related to the machine tool itself. If the structure of the machine tool is unstable or the accuracy is not high enough, it will be difficult to ensure that no vibration marks appear during processing. The solution to this problem is to replace the machine tool with a more stable and precise one.
In short, vibration marks on the outer diameter of CNC vertical lathes are caused by a combination of factors. To solve this problem, it is necessary to consider and improve many aspects such as cutting tools, workpiece materials, processing procedures and machine tools to ensure processing quality and efficiency.