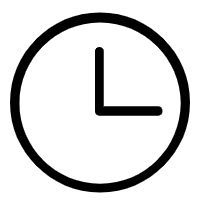
There may be many reasons for tool collision failure in CNC turning and milling composite machines. The following are some common possibilities:
1.Program error:
Wrong CNC program or tool path planning of the machine tool can cause the tool to collide with the workpiece. Ensure that procedures are correct, complete, and carefully verified and simulated.
2. Wrong workpiece or fixture position:
If the machine tool workpiece or fixture is not clamped correctly, or errors are made in the positioning of the workpiece and fixture, it may cause the tool to collide with the workpiece.
3. Tool length and radius deviation:
The actual length and radius of the machine tool tool do not match the values defined in the program, which may cause tool collision failure. Ensure tool parameters are accurate and conduct regular measurements and inspections.
4. Tool wear or damage:
Using severely worn or damaged tools on machine tools may cause tool collisions. Replace worn tools in a timely manner and ensure that the quality of the tools meets requirements.
5. CNC system failure:
Errors or malfunctions in the machine tool's CNC system can lead to errors, which can lead to tool collisions. Check the alarm information of the CNC system to ensure the normal operation of the system.
6. The tool deviates from the center trajectory:
The dynamic characteristics of CNC turn-milling machine tools, machine tool rigidity, and the state of the guide rails may cause the tool to deviate from the center trajectory during motion, resulting in tool collision. Perform machine tool maintenance and calibration to ensure stable machine tool performance.
7. Too fast:
When the machine tool is cutting at high speed, especially in turns or corners, too fast a speed may cause the tool to be unable to adapt in time, resulting in tool collision. Adjust the cutting parameters appropriately to ensure that the speed matches the dynamic response of the machine tool.
8. Workpiece deformation:
During the cutting process of the machine tool, the workpiece may be deformed due to material properties or improper clamping, resulting in tool collision. Pay attention to the stability and accuracy of workpiece clamping.
9. Lack of effective security measures:
The lack of effective safety measures and emergency stopping systems in machine tools may cause the tool to continue to move and cause tool collision. Make sure there is an emergency stop button on the CNC machine and provide training to ensure operators understand emergency procedures.
Regular machine tool maintenance, tool inspections and personnel training are all key factors when it comes to preventing and resolving tool collision failures. Timely fault diagnosis and correction can improve the working stability and safety of CNC turning and milling compound machine tools.