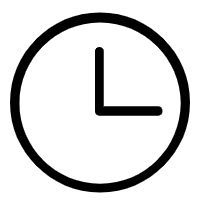
When CNC lathes process workpieces, the choice of clamping method is crucial to the processing results and workpiece quality. The following are several common CNC lathe workpiece clamping methods:
1. Three-jaw chuck clamping: This is one of the most common clamping methods for CNC lathes. Three-claw chuck is usually used for clamping round workpieces. By adjusting the clamping force and position of the three-claw chuck, the workpiece is clamped in the center to ensure the rotational stability of the workpiece.
2. Four-claw chuck clamping: CNC lathe four-claw chuck is often used for clamping irregularly shaped or square workpieces. The number of claws of the four-jaw chuck increases the clamping force of the workpiece, making it more suitable for processing workpieces that require higher clamping force.
3. Universal joint clamping: Universal joint clamping of CNC lathes is suitable for certain workpieces with complex and irregular shapes. By adjusting the angle and position of the universal joint, multi-directional clamping of the workpiece is achieved and the stability of the processing is improved. performance and precision.
4. Direct clamping: CNC lathe direct clamping is usually used for small, simple-shaped workpieces. Fixing the workpiece directly on the workbench or workbench through a clamping device or fixture is simple and fast, and is suitable for some occasions with low processing requirements.
5. Indexing head clamping: CNC lathe indexing head clamping is suitable for workpieces that require rotational symmetry, such as gears. Through the rotation and positioning functions of the indexing head, the rotation and positioning of the workpiece during processing is realized, ensuring the symmetry and accuracy of CNC lathe processing.
6. Vacuum adsorption clamping: CNC lathes can use vacuum adsorption clamping for some flat or thin plate-shaped workpieces. By creating a vacuum adsorption force on the workbench, the workpiece is fixed on the workbench, which is suitable for situations where clamps or fixtures are not allowed during processing.
7. Positioning pin clamping: The CNC lathe can reserve positioning pin holes on the workpiece that needs to be positioned and processed, and set corresponding positioning pins on the workbench of the CNC lathe to accurately position the workpiece to ensure the accuracy and consistency of processing. sex.
These clamping methods can be selected and combined according to the shape, size and processing requirements of the CNC lathe workpiece to ensure the stability, accuracy and safety of the processing process.