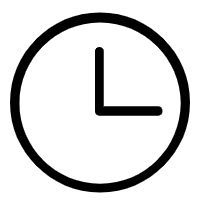
The CNC vertical lathe tool setter is a very practical CNC machine tool accessory. Its function is to achieve precise tool setting of the workpiece in the CNC vertical lathe to ensure processing quality and efficiency. The detailed steps of CNC vertical lathe tool setting will be introduced in detail below.
1. Determine the tool setting tool
First, you need to determine the tool that needs to be used for tool setting to ensure the precision and accuracy of tool setting. The selection of tool setting tools should take into account the tool diameter and length, as well as the characteristics and requirements of the workpiece processing.
2. Install the tool
Install the selected tool on the CNC vertical lathe and adjust it to meet the tool setting requirements. The adjustment process mainly includes the insertion depth, inclination angle, rotation direction, etc. of the tool.
3. Coarse tool setting
Coarse tool setting is the first step in the tool setting process, and its purpose is to roughly align the tool with the workpiece. The specific operation steps are: first use a caliper to measure the distance between the upper end of the tool and the workpiece surface, and then adjust the X and Z axis coordinates according to the distance so that the tool can quickly contact the workpiece surface.
4. Fine-tuning the tool setting
Fine adjustment of the tool setting is a key step in the tool setting process. Fine adjustment of the workpiece is achieved by adjusting the tool setting parameters in the CNC system. If the tool inclination angle is too large, you can make it more horizontal by reducing the adjustment parameter value; if the tool height is low, you can adjust it to the correct height by increasing the adjustment parameter value. During the adjustment process, the corresponding test procedures can be continuously adjusted to obtain more accurate tool setting results.
5. Verify tool setting
After passing the tool calibration, the tool calibration results need to be verified to ensure that the tool calibration results meet the requirements. During tool calibration verification, you can use the simulation program on the CNC vertical lathe to check the machining path, or conduct actual processing tests to check the dimensional errors of the processing to determine the correctness of the tool calibration results.
6. Adjust parameters
If the tool calibration results do not meet the requirements, the tool calibration parameters need to be readjusted for optimization. Common adjustment parameters include: tool height deviation parameters, inclination angle deviation parameters, X, Z axis coordinate values, etc. By continuously adjusting the parameters, perform tool calibration again until satisfactory tool calibration results are obtained.
To sum up, CNC vertical lathe tool setting is a very important process link and has a significant impact on processing quality and efficiency. Only through strict tool setting steps and processes can the correctness and accuracy of the tool setting results be guaranteed, thereby providing a solid technical guarantee for effective CNC machining.