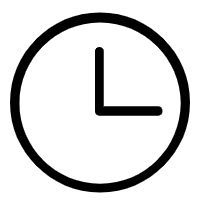
The spindle of a CNC vertical lathe is a key processing component, and its maintenance is crucial to ensuring the normal operation and processing accuracy of the machine tool. The following are the maintenance methods of CNC vertical lathe spindle:
1. Lubrication system maintenance: CNC vertical lathe spindles are usually equipped with a dedicated lubrication system, including bearings and gears. Regularly check the quality and quantity of lubricating oil to ensure the normal operation of the CNC vertical lathe lubrication system. Change the lubricant at the manufacturer's recommended intervals to prevent excessive bearing wear and insufficient oil lubrication.
2. Check the bearings: CNC vertical lathes regularly check the status of the spindle bearings, including the temperature, noise and vibration of the bearings. If any abnormality is found, repair or replace the bearing in time. Ensure that the CNC vertical lathe bearings are in good condition to ensure the stability and life of the spindle.
3. Clean the spindle: CNC vertical lathes regularly clean the spindle surface, especially the spindle taper hole and spindle taper seat, to ensure that cutting fluid and chips do not affect the accuracy and stability of the spindle. Use detergent and a soft cloth to clean, and avoid using substances that are corrosive to the spindle.
4. Check the cooling system regularly: If the CNC vertical lathe spindle is equipped with a cooling system, check the flow and temperature of the coolant regularly. Maintain the normal operation of the CNC vertical lathe cooling system to prevent the spindle from being damaged due to overheating.
5. Avoid overload operation: CNC vertical lathe should avoid operating the spindle in an overloaded state. Reasonably set cutting parameters to ensure appropriate feed and speed of the tool and workpiece to prevent wear and damage caused by excessive load on the spindle.
6. Regularly check the geometric accuracy of the spindle: CNC vertical lathes use measuring instruments, such as micrometers or laser measurement systems, to regularly check the geometric accuracy of the spindle. CNC vertical lathes include concentricity, axial runout, etc. Adjust or calibrate as needed to ensure spindle machining accuracy.
7. Perform regular balance checks: The balance state of the CNC vertical lathe spindle directly affects the stability and life of the machine tool. Regularly use a balance detection instrument to check the balance of the spindle. If any imbalance is found, perform balance correction in time.
8. Operator training: Provide training to CNC vertical lathe operators to learn the correct use and operation methods. Avoid incorrect operations such as over-machining or sudden changes in cutting load to reduce impact and damage to the spindle.
Combining the above measures can ensure the stable operation of the CNC vertical lathe spindle, extend the spindle life, and improve the production efficiency and processing accuracy of the machine tool.