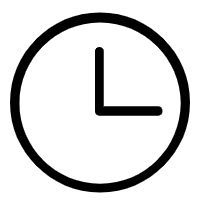
Choosing cutting tools for CNC lathes is one of the important steps to ensure efficient and accurate machining. The selection of cutting tools involves many factors such as workpiece material, processing requirements, and cutting conditions. Here are some suggestions to help you choose the right tool for your CNC lathe:
1. Understand the workpiece material: Different workpiece materials for CNC lathes require different types of cutting tools. For example, for metallic materials, carbide knives are typically used, whereas for plastics or composites, a single-edged or multi-edged knife may be required.
2. Understand the cutting requirements: The selection of CNC lathe tools should consider the processing requirements, such as roughing or finishing, high-speed cutting or heavy-duty cutting. Choose the appropriate tool type based on your cutting requirements.
3. Choose the appropriate tool material: The choice of CNC lathe tool material directly affects its life and performance. Common tool materials include carbide, high-speed steel, ceramics, etc. Carbide is often used for high-speed cutting, while high-speed steel is suitable for general cutting.
4. Determine the tool shape: The shape of the CNC lathe tool is closely related to the processing characteristics. For example, flat nose cutters are suitable for flat surface machining, ball nose cutters are suitable for spherical surface machining, and spiral cutters are suitable for efficient cutting.
5. Consider tool coating: CNC lathe tool coating can improve the hardness, wear resistance and thermal conductivity of the tool. Common coatings include titanium carbide (TiC), aluminum oxide (Al2O3), etc. Select the appropriate coating based on the specific application.
6. Understand the number of tool edges: The number of edges of CNC lathe tools affects cutting efficiency and surface quality. Generally speaking, multi-edged knives are suitable for efficient cutting, while single-edged knives are suitable for some special processing requirements.
7. Match the tool holder and clamping system: The design of the CNC lathe tool holder and clamping system is also very important. Make sure the tool holder and clamping system match the specifications of the CNC lathe to prevent loose or unstable tools.
8. Consider cooling and chip removal: When CNC lathes are performing high-speed cutting or heavy-load cutting, the cooling and chip removal functions become particularly important. Choose a tool with good cooling design and chip evacuation.
9. Reference cutting parameters: CNC lathe tool manufacturers usually provide applicable cutting parameters, including cutting speed, feed rate and depth of cut. Make sure you choose the right tool based on these parameters.
10. Maintenance and inspection: Regular inspection and maintenance of CNC lathe cutting tools to maintain their sharpness and timely replacement as needed. Regular tool coating inspection is also an important part of maintaining tool performance.
Taking the above factors into consideration, choosing tools suitable for specific processing needs can improve the processing efficiency and processing quality of CNC lathes. When making tool selection, it is best to consult the tool manufacturer or supplier for professional advice.