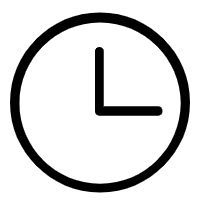
The process of clamping workpieces on a CNC lathe can be divided into the following steps:
1. Preparation:
Prepare the CNC lathe workpiece and fixture, ensure the surface of the workpiece is clean, and select the appropriate fixture for clamping.
Prepare the required tools, and prepare the processing program and cutting parameters according to the processing technology.
2. Select the fixture:
Select the appropriate fixture according to the shape, size and processing requirements of the CNC lathe workpiece. The fixture should be able to hold the workpiece firmly and ensure that the workpiece does not move or shake during processing.
3. Clamp the workpiece:
Place the CNC lathe workpiece on the fixture, and select the appropriate clamping method according to the shape and processing requirements of the workpiece. Common clamping methods include mechanical clamping, pneumatic clamping, hydraulic clamping, etc.
Ensure that the contact surface between the CNC lathe workpiece and the fixture is clean and flat, and the clamping force is evenly distributed to avoid deformation or damage of the workpiece.
5. Knife setting:
CNC lathes use cutting tools to precisely position workpieces and tool setting. By adjusting the position of the tool and the height of the tool tip, the tool is correctly aligned with the workpiece surface to ensure machining accuracy and quality.
Use a special tool setting instrument or the tool setting function that comes with the CNC lathe to perform tool setting operations.
6. Fixture correction:
After clamping the workpiece on the CNC lathe, the fixture is calibrated to ensure that the position and clamping force of the fixture meet the requirements. Make corrections by checking whether the fixing bolts of the fixture are loose and whether the clamping force of the fixture is uniform.
7. Processing verification:
CNC lathes perform processing verification before formal processing. Through processing verification in manual mode or trial cutting mode, check the collision between the workpiece and the tool, the correctness of the processing path, etc. to ensure that no abnormalities occur during the processing.
8. Start processing:
When it is confirmed that the workpiece clamping and processing preparations have been completed and there are no abnormal conditions, the CNC lathe can be started for formal processing. Start automatic processing operations according to the preset processing program and cutting parameters.
9. Monitor processing:
During the processing of CNC lathes, the processing status and processing quality are regularly monitored. Pay attention to the cutting conditions, tool wear and surface quality of the workpiece, and adjust the processing parameters or replace the tool in a timely manner to ensure that the processing effect meets the requirements.
Through the above steps, the workpiece clamping operation of the CNC lathe can be effectively performed to ensure the safety, accuracy and stability of the processing process.