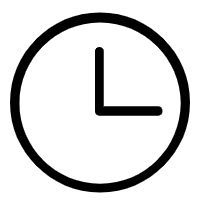
The division of CNC lathe machining processes usually involves multiple steps, each with its own specific tasks and goals. The following are the main divisions of CNC lathe processing procedures under normal circumstances:
1. Design and planning:
Part Design: CNC Lathe During this stage, engineers design the geometry and dimensions of the part, taking into account the properties of the material and the requirements of the final product.
Process planning: Determine the CNC lathe processing technology, including selecting tools, cutting parameters, processing sequence, etc.
2.CAD/CAM programming:
Part Modeling: CNC lathes use computer-aided design (CAD) software to model parts.
Tool path planning: CNC lathes use computer-aided manufacturing (CAM) software to generate CNC programs to determine the movement trajectory and processing path of the tool.
3. CNC program settings:
Set process parameters: Enter cutting speed, feed speed, tool cutting depth and other parameters in the CNC system.
Program debugging: Verify the correctness of the CNC lathe CNC program to ensure that the lathe can process as expected.
4. Material preparation and clamping:
Material preparation: CNC lathes prepare raw materials, usually metal blanks, to ensure they meet design requirements.
Clamping workpieces: CNC lathes use clamps to securely hold workpieces to the CNC lathe to ensure machining accuracy and safety.
5. Rough machining:
Rough Turning: A CNC lathe uses appropriate cutting tools to perform the initial removal of excess material and create an approximate shape.
Rough milling: A CNC lathe performs rough milling operations where necessary to make the surface smoother.
6. Semi-finishing:
Semi-finish turning: CNC lathes use smaller tools to perform fine turns that gradually approach the final shape.
Semi-fine milling: CNC lathes perform a semi-fine milling process to improve surface quality.
7. Finishing:
Finish turning: CNC lathes use small tools to perform final fine turning to achieve the geometry and size required by the design.
Fine Milling: A CNC lathe performs the final fine milling to improve surface finish and dimensional accuracy.
8. Testing and quality inspection:
Dimensional measurement: CNC lathes use measuring tools to check whether the dimensions of the part meet the design requirements.
Surface quality inspection: Check the surface finish and quality of CNC lathe parts.
9. Cleaning and protection:
Clean the workpiece: The CNC lathe removes chips and oil residue generated during the machining process.
Protective treatment: CNC lathes undergo anti-corrosion, anti-rust and other treatments according to specific requirements.
10. Packaging and delivery:
Packaging: CNC lathes take appropriate packaging measures to ensure that parts are not damaged during transportation.
Delivery: The CNC lathe delivers the finished part to the next manufacturing stage or to the end user.
These steps may vary based on specific manufacturing needs and part characteristics, but overall, they form the basic flow of a CNC lathe machining operation.