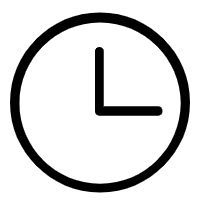
The tool setting operation of the double-column CNC vertical lathe is a key step to ensure processing accuracy and efficiency. The following are the basic steps for tool setting:
1. Tool setting:
Prepare the tool setter for the double-column CNC vertical lathe and place it on the tool holder.
The lathe returns to the mechanical origin.
For double-column CNC vertical lathes, install a tool holder in the tool holder and align it with the tool setter. Rotate the tool holder until it contacts and is fixed with the bayonet of the tool setter.
When exchanging each tool of a double-column CNC vertical lathe, a tool setting operation is required. Different types of tool setting operations are performed according to the machine tool operation manual.
2. Tool tip to tool:
For the double-column CNC vertical lathe, prepare the tip base or right-angle plate and place it as far as possible above the turning tool, and at the same time turn on the hydraulic oil pump switch.
For double-column CNC vertical lathes, move the turning tool axis outside the cutting edge and observe the gap between the tool tip and the tip seat or right-angle plate.
The double-column CNC vertical lathe adjusts the bearing seat according to the gap size and fixes it firmly until the tool tip contacts the tip seat or right-angle plate and can be fixed.
Finally, the tool alignment between the adjacent tool tip and the adjacent supporting surface is performed.
3. Direct tool setting:
For double-column CNC vertical lathe, select the center of the right end face of the part as the tool setting point and set it as the zero point. After the machine tool returns to the origin, each tool that needs to be used is calibrated with the center of the right end face of the part as the zero point.
When the tool contacts the right end face, enter Z0 and click Measure. The measured value will be automatically recorded in the tool offset value, indicating that the Z-axis tool calibration is completed.
X-axis tool setting is for trial cutting. Use a tool to turn a small amount of the outer circle of the part. Measure the value of the outer circle to be turned (for example, x is 20mm) and enter x20. Click measurement. The compensation value of the double-column CNC vertical turning tool will automatically record the measured value. Value, now the x-axis is also correct.
4. Auxiliary tool setting:
Prepare the auxiliary tool setter and adjust it according to the instructions.
The double-column CNC vertical lathe selects the corresponding auxiliary tool setting tool according to the material to be cut.
The double-column CNC vertical lathe inserts the tool into the lathe's cutting edge, and sets an auxiliary tool setter above the turning tool.
The double-column CNC vertical lathe adjusts its position so that the cutting part of the tool contacts the auxiliary instrument and moves the turning tool until the tool setting is completed.
5. Recording and inspection:
Input the measured x, y, z values into the machine tool workpiece coordinate system storage address G5* (generally use G54~G59 codes to store tool setting parameters).
Enter the panel input mode (MDI), enter "G5*", press the start key (in automatic mode), and run G5* to take effect.
Check whether the tool setting is correct to ensure processing accuracy.
Please note that these steps are general guidance and may vary depending on machine model, control system, and specific machining needs. Therefore, in actual operations, the machine tool operating manual and relevant safety regulations should be strictly followed to ensure the accuracy and safety of tool setting operations.