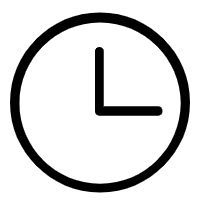
In order to reduce the impact of thermal deformation of CNC lathes, the following measures can be taken:
1. Control heat sources: Reduce heat sources inside and outside the CNC lathe as much as possible. For example, heat sources such as electric motors, gearboxes, hydraulic devices, and fuel tanks are separated from the main engine to reduce heat generation. For heat sources that cannot be separated from the main engine, such as spindle bearings, screw nut pairs, etc., heat generation can be reduced by improving their friction characteristics and lubrication conditions.
2. Enhance heat dissipation: Install heat dissipation devices, such as fans, heat sinks, etc., on the heating parts of the CNC lathe to enhance the heat dissipation effect. At the same time, maintain good ventilation around the CNC lathe so that the heat can be discharged in time.
3. Control temperature rise: CNC lathes reduce the heat generated during the cutting process by adjusting cutting parameters and using coolant. In addition, heating can also be used in the low-temperature part of the CNC lathe to make the temperature of each point of the CNC lathe consistent to reduce warpage deformation caused by temperature differences.
4. Improve machine tool structure: When designing CNC lathes, thermal deformation factors should be fully considered. For example, the use of thermally symmetrical structural design allows the machine tool to maintain better stability when heated. At the same time, the layout and structural design of the machine tool should be optimized to reduce the transfer and accumulation of heat inside the machine tool.
5. Thermal compensation technology: CNC lathes use thermal compensation technology to offset the effects of thermal deformation. For example, a thermal compensation program is set up in the CNC system to automatically adjust the processing parameters and tool compensation amount according to the actual temperature changes of the machine tool to maintain the stability of processing accuracy.
6. Select appropriate materials and tools: CNC lathes choose materials with small thermal expansion coefficients and good thermal conductivity to manufacture key components of the machine tool, such as spindles, lathes, etc. At the same time, choose tools suitable for the material being processed to reduce the heat generated during the cutting process.
7. Regular inspection and maintenance: Regular inspection and maintenance of CNC lathes, such as cleaning the surface and interior of the machine tool, checking and tightening the connections of various components, replacing worn parts, etc., to maintain the good condition of the machine tool.
Through the implementation of the above measures, the impact of thermal deformation of CNC lathes can be effectively reduced, and the processing accuracy and service life of the machine tools can be improved.