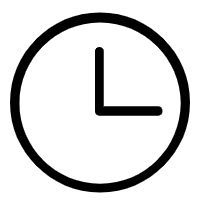
Reducing the processing errors of CNC lathes is one of the keys to improving product quality and processing efficiency. Here are some common methods and tips that can help reduce machining errors on CNC lathes:
1. Machine tool maintenance: CNC lathes should be maintained and maintained regularly to ensure the accuracy and stability of each component of the machine tool. Including cleaning and adjustment of lubrication system, transmission system, guide rail, etc.
2. Tool selection and regular replacement: Select appropriate tools for CNC lathes, and regularly replace severely worn tools. The selection and status of the tool directly affect the machining accuracy and surface quality.
3. Optimization of processing parameters: CNC lathes optimize parameters such as cutting speed, feed speed, and cutting depth in the processing program. Reasonable processing parameters can reduce errors caused by thermal deformation, vibration, etc.
4. Workpiece clamping and fixture design: CNC lathes adopt reasonable workpiece clamping methods and fixture design to ensure that the workpiece is firmly clamped on the machine tool. Unstable clamping can lead to machining errors.
5. Environmental control: CNC lathes control the temperature and humidity of the processing environment to reduce the impact of thermal deformation of the machine tool on processing accuracy under different temperature and humidity conditions.
6. Tool cutter compensation: CNC lathes use the tool cutter compensation function to compensate based on actual processing conditions to correct errors caused by tool wear.
7. CNC system calibration: CNC lathes regularly calibrate the CNC system to ensure that the instructions output by the CNC system are consistent with the actual machine tool movement. This includes calibrating tool lengths, workpiece coordinate systems, etc.
8. Workpiece preheating: For some special materials or large workpieces, CNC lathes can consider moderately preheating the workpiece before processing to reduce errors caused by temperature changes during processing.
9. Real-time monitoring and adjustment: Use the real-time monitoring function of CNC lathes to promptly discover abnormalities in processing and make adjustments to avoid the accumulation of errors.
10. Employee training: Provide professional training to CNC lathe operators so that they can master the use of CNC systems and machine tool operating skills to reduce errors caused by human factors.
By comprehensively considering these factors, the processing errors of CNC lathes can be effectively reduced and the processing accuracy and product quality can be improved.