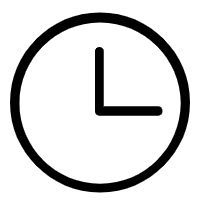
Using tool radius compensation is an important function in CNC lathe processing. It can help correct the difference between the actual radius of the tool and the radius set in the program, thereby improving machining accuracy. Here are some things to note when using tool radius compensation:
1. Correct tool radius value: In CNC lathe CNC programming, ensure that the actual tool radius value is entered correctly. Wrong values can lead to machining errors, so the geometric parameters of the tool should be carefully checked and verified.
2. Wear compensation: CNC lathe tools will wear during use, and CNC lathes usually support wear compensation functions. Regularly check the wear degree of the cutting tools and make appropriate compensation according to the actual situation.
3. Compensation direction: CNC lathe tool radius compensation has positive and negative directions, usually based on the tool tip, and the positive direction is outside the tool tip. In CNC programming, make sure to select the correct compensation direction to prevent machining errors.
4. Cutting direction: Different cutting directions of CNC lathes may require different tool radius compensation values. Pay attention to correctly setting the cutting direction in the program to avoid processing errors in different directions.
5. Workpiece coordinate system and tool radius compensation: In CNC lathe CNC programming, the choice of workpiece coordinate system will affect the results of tool radius compensation. Ensure the correct selection of the CNC lathe workpiece coordinate system so that the compensation values take effect as expected.
6. Cutting speed and feed speed: Changes in the cutting speed and feed speed of CNC lathes may affect the wear of the tool, which in turn affects the effect of tool radius compensation. When changing the speed, you need to consider whether the tool radius compensation value needs to be adjusted.
7. Reasonable tool path planning: Reasonable tool path planning for CNC lathes can reduce changes in cutting force, thereby slowing down tool wear. Consider tool paths in programming to maximize tool performance.
8. Real-time monitoring and adjustment: During the actual processing of CNC lathes, by monitoring the processing results in real time, tool wear or other problems can be discovered in time, and the tool radius compensation value can be adjusted as needed.
In general, when using tool radius compensation, you need to carefully set parameters, regularly check tool wear, reasonably plan tool paths, and perform real-time monitoring and adjustment when necessary to ensure machining accuracy and efficiency.