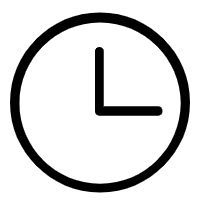
CNC lathe processing of parts usually includes the following basic steps:
1. Design and planning:
Before CNC lathes start processing parts, they need to design and plan the parts. This includes determining the part’s geometry, dimensions, materials, and machining processes. Design is usually done using computer-aided design (CAD) software.
2.Write CNC program:
Once the design of the CNC lathe is completed, a CNC program needs to be written. A CNC program is a series of instructions that tell the CNC lathe how to cut and process. These programs are usually written using CNC programming languages such as G-code and M-code.
3. Set the working coordinate system:
On a CNC lathe, you need to set the working coordinate system, that is, determine the starting point and relative position of the part. This helps ensure that the coordinates in the program match those on the actual machine tool.
4. Install and clamp the workpiece:
The CNC lathe installs the raw material to be processed (usually a metal blank) on the CNC lathe and clamps it with a clamp to ensure stability during the processing. Fixture selection and installation are critical to maintaining the accurate position of the part.
5. Clamping tools:
CNC lathes install and hold cutting tools (tools, drill bits, etc.) according to the requirements of the processing program. Tool selection depends on the required cutting operation and the geometric characteristics of the part.
6. Debugging and testing:
Before the CNC lathe is officially processed, some trial runs and tests are performed to ensure the correctness of the CNC program and the normal operation of the machine tool. This may involve manual motion, dry runs, and checking tool paths.
7. Start processing:
After the CNC lathe is ready, start the CNC program and the CNC lathe will automatically process according to the predetermined path and cutting parameters. At this stage, the machine tool's servo system is responsible for controlling the movement of each axis to achieve precise cutting.
8. Monitoring and quality control:
During the processing process, the CNC lathe monitors the operating status of the machine tool to ensure that the size and surface quality of the parts meet the specified requirements. Measure and adjust if necessary.
9. Uninstall and organize:
After the CNC lathe is completed, unload the processed parts and perform necessary sorting and cleaning work. This may include removal of residual material, chips, etc.
10. Quality inspection and acceptance:
CNC lathes perform final quality inspections to ensure parts meet design requirements. This may involve using measuring tools, checking surface quality, etc.
Each of these steps is critical to the quality and accuracy of the final part. The automation and precision control of CNC lathes make the machining process more efficient and controllable.