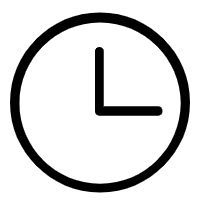
The CNC horizontal machining center, as a representative of high-end manufacturing equipment, reflects the deep integration of modern mechanical engineering and information technology in its system composition, covering multiple subsystems such as control, drive, machinery, and detection. The following is a detailed explanation of the composition of this complex system:
1. CNC System
The CNC system is the "brain" of the entire machining center, responsible for receiving machining programs from computer-aided design (CAD) and computer-aided manufacturing (CAM) systems, and converting these programs into precise motion instructions through complex algorithms. The core components include high-performance processors, memory, input/output interfaces, and human-computer interaction interfaces. The mainstream CNC systems in the current market, such as Siemens 840D and Fanuc 30i, have high-speed processing capabilities, high-precision control, and a friendly operating interface, supporting multi axis linkage, high-speed cutting, and other functions.
2. Servo Drive System
The servo drive system responds to the instructions of the CNC system, accurately controls the speed and position of the motor, and then drives the linear or rotational motion of each axis. The system includes servo drivers, servo motors, and feedback devices (usually encoders). High response speed and precision are the basic requirements of servo systems, ensuring precise tracking of tool paths during the machining process, thereby achieving micrometer level machining accuracy.
3. Mechanical Structure
The mechanical structure of a horizontal machining center is the foundation of its stability and accuracy. It mainly consists of a bed, columns, worktable, spindle box, feed mechanism, etc. The bed and columns are usually made of high-strength cast iron material, which has undergone precision processing and aging treatment to ensure stability and shock absorption effect under long-term use. The workbench can be fixed or have a rotating function to achieve multi sided machining. The spindle unit can be equipped with a direct drive motor or gear drive according to processing requirements, providing high torque or high speed.
4. Automatic Tool Change (ATC) system
The automatic tool change system is a key component for improving the efficiency of machining centers, allowing for quick tool change without interrupting the machining process. ATC usually includes a tool magazine, a tool changing arm, and corresponding driving mechanisms. The tool library stores multiple types of tools, and the tool changing arm completes the tool retrieval and insertion actions through precise mechanical and electronic control, ensuring the continuity of the machining process.
5. Measurement&Compensation System
In order to maintain machining accuracy, the horizontal machining center is also equipped with various detection and compensation systems. For example, online detection of tool length and wear, monitored in real-time through sensors, ensures the accuracy of machining dimensions; The thermal deformation compensation function automatically adjusts processing parameters based on temperature changes in various parts of the machine tool, reducing errors caused by thermal expansion.
6. Auxiliary Systems
In addition to the core systems mentioned above, it also includes auxiliary facilities such as cooling systems, lubrication systems, chip removal systems, and protective devices. The cooling system is used to reduce the heat generated during the cutting process and extend the tool life; The lubrication system ensures low friction and long service life of moving parts; The chip removal system promptly cleans up cutting waste and maintains a clean processing environment; Protective devices are designed to ensure the safety of operators.
In summary, the system composition of CNC horizontal machining centers is a highly integrated and collaborative complex, and the design and optimization of each part are aimed at maximizing machining efficiency, accuracy, and reliability, meeting the processing needs of modern manufacturing for high-quality and highly complex parts.