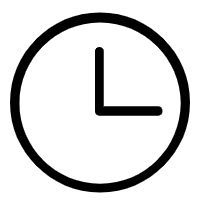
The impact of thermal deformation on the accuracy of automatic CNC lathe systems is an important consideration. Thermal deformation can have a negative impact on machine tools, workpieces and tools, thereby affecting machining accuracy. The following are the main hazards of thermal deformation to accuracy:
1. Machine tool deformation: Due to thermal expansion of CNC machine tools, various components of the machine tool may deform, resulting in instability or distortion of the machine tool structure. This will affect the relative position of the tool and workpiece, thereby reducing machining accuracy.
2. Workpiece deformation: During CNC machine tool processing, the workpiece may undergo thermal deformation due to the influence of heat, especially during high-speed cutting and high-temperature processing. This can lead to deviations in the shape of the workpiece, making it inconsistent with design requirements.
3. Tool wear: High temperature will increase the wear rate of CNC machine tool tools, especially during high-speed cutting. Tool wear will lead to instability of cutting force and reduction of cutting quality, thus affecting machining accuracy.
4. Measurement error: Thermal deformation of CNC machine tools may affect the accuracy of the measurement equipment, causing deviations in the dimensional measurement results of the processed workpiece, thus affecting the final processing accuracy assessment.
In order to reduce the harm of thermal deformation to machining accuracy, the following measures can be taken:
1. Temperature control: Maintaining a stable temperature environment for CNC machine tools is the key to reducing thermal deformation. This can be achieved through workshop air conditioning, machining fluid cooling systems, etc.
2. Tool and process selection: CNC machine tools select appropriate tool materials and cutting processes to reduce heat accumulation and cutting heat during the machining process.
3. Processing strategy optimization: CNC machine tools optimize processing strategies, such as reducing cutting speed, increasing cutting lubrication, etc., to reduce heat accumulation and thermal deformation.
4. Tool cooling: CNC machine tools use tool cooling systems to take away heat from the cutting area in a timely manner, reduce tool temperature, and slow down tool wear.
5. Monitoring and compensation: CNC machine tools use monitoring equipment such as temperature sensors to monitor temperature changes of the machine tool and workpiece, and adjust processing parameters in real time through the CNC system to compensate to maintain processing accuracy.
In summary, reasonable management of thermal deformation is the key to ensuring the accuracy of fully automatic CNC machine tool lathe systems. By comprehensively applying a variety of measures, the impact of thermal deformation on machining accuracy can be minimized.