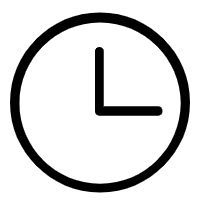
There are a variety of failures that can occur with a CNC lathe spindle, some of the common ones include:
1. Spindle overheating: Long-term high-load operation of CNC lathes or poor lubrication may cause the spindle to overheat. This may be caused by lubrication system failure, spindle bearing damage, or improper tool installation.
2. Spindle bearing damage: Damage to the CNC lathe spindle bearing may cause the spindle to run unstable, produce abnormal noise or vibration, which may be caused by long-term use, overload operation or poor lubrication.
3. Spindle vibration: CNC lathe spindle vibration may lead to reduced processing quality or increased tool wear, which may be caused by unbalanced tools, damaged spindle bearings, or unstable spindle installation.
4. Spindle transmission system failure: Failures in the CNC lathe spindle transmission system may include loose belts, damaged gears, or broken transmission chains, etc., which may cause the spindle speed to be unstable or unable to operate normally.
5. Spindle cooling system failure: Failure of the CNC lathe spindle cooling system may cause the spindle to overheat, which may be caused by cooling water pump failure, cooling pipe blockage, or insufficient coolant.
6. Spindle gearbox failure: Failure of the CNC lathe spindle gearbox may cause the spindle speed to be unable to be adjusted normally or the rotation speed to be unstable. This may be caused by damaged gearbox parts or insufficient oil.
7. Spindle motor failure: A CNC lathe spindle motor failure may cause the spindle to fail to operate normally or the speed to be unstable. This may be caused by a short circuit in the motor winding, a motor driver failure, or a power supply problem.
The above are some common CNC lathe spindle failures. Regular inspection and maintenance can reduce the occurrence of these failures and ensure the normal operation of the CNC lathe.