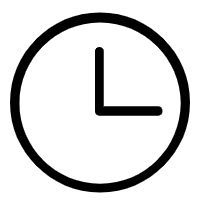
CNC vertical lathe is an extremely precise machine tool, and its use requires a high-precision spindle. The spindle must operate within a certain temperature range to ensure its normal operation and long-term stability. This is why the CNC vertical lathe spindle heats up.
Spindle heating refers to controlling the spindle temperature through the heating system to raise its temperature to a suitable range. Spindle heating may involve various technologies, such as water cooling, air cooling, electric heating, etc. During the machining process, frictional heat will be generated after contact between the machined parts and the spindle. If the spindle is not heated, the spindle temperature will be too low, which will affect the stability and processing accuracy of the machine tool, resulting in excessive dimensional errors and rough surfaces of the workpiece. adverse effects and other negative effects.
Normally, the spindle heating is designed based on the usage requirements of the machine tool. The spindle heating time and temperature should be calibrated to the optimal state to achieve high accuracy and efficiency. Spindle temperature control technology should also fully consider factors such as ambient temperature, machine tool running time, and thermal effects around the machine tool.
When processing has to be suspended while the spindle is heating up, appropriate measures need to be taken to avoid damage to the spindle due to sudden cooling. The spindle heating and downtime should be reasonably arranged to ensure the long-term stability of the spindle.
In daily use, we should always pay attention to the temperature changes of the spindle, detect abnormal situations in time, and solve them in time. If the spindle is overheated or undercooled, we need to operate it correctly and adjust the appropriate temperature to protect the smooth operation of the machine tool and improve processing accuracy and efficiency. Therefore, the heating of the CNC vertical lathe spindle is particularly important in use.