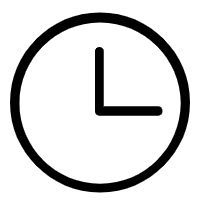
A machining center is a type of CNC machine tool and is a device used to process parts. Generally speaking, machining centers can be divided into three-axis and four-axis machining centers according to different number of axes. So, what are the differences between three-axis and four-axis machining centers?
First of all, the different number of axes represents the number of controllable directions of movement. The three-axis machining center can only move in three directions, namely X, Y, and Z directions. The four-axis machining center adds a rotation axis on this basis, which can control the rotation of the part so that it is not subject to processing constraints and facilitates processing at any angle.
Secondly, four-axis machining centers have higher machining accuracy and efficiency. Because it can be processed freely at different angles, it is more comfortable when processing complex curved surfaces, three-dimensional curves and other structures. And while avoiding possible tool collisions, it can also save processing time to the maximum extent.
Finally, four-axis machining centers are essential in certain machining fields. For example, in the fields of engraving, mold processing, and automobile engine block processing, four-axis machining centers can have greater advantages.
Of course, compared with three-axis machining centers, four-axis machining centers are also different in price. Therefore, you need to make a clear analysis and judgment of your personal needs before making a purchase, and you cannot blindly follow trends or blindly pursue high-end equipment.
To sum up, the three-axis machining center is one of the common CNC machining equipment, while the four-axis machining center is relatively high-end and can help production companies improve efficiency, reduce costs and improve part accuracy. For different processing needs, it is most important to choose a machining center that suits you.