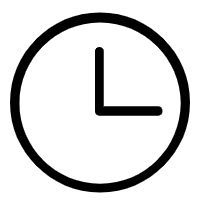
In today's highly automated manufacturing environment, CNC lathes have become the core equipment for precision machining. But many factors may affect its processing accuracy, one of which is thermal deformation. Thermal deformation refers to the deformation of various parts of the lathe due to temperature changes, which in turn affects the machining accuracy.
First, we need to understand the effect of temperature on metals. Metal will deform to a certain extent at high temperatures due to the thermal expansion coefficient of the metal. When the lathe is running at high speed, various parts of the metal generate a large amount of heat due to friction and cutting, and this heat may cause slight deformation of the lathe structure. Especially when processing long tools or deep holes, heat accumulation is more obvious.
The influence of thermal deformation on machining accuracy is mainly reflected in the following aspects:
1. Dimensional accuracy: Thermal deformation may cause the distance between the tool tip and the workpiece to change, affecting the cutting accuracy and thus the dimensional accuracy of the workpiece.
2. Contour accuracy: Thermal deformation may change the cutting path of the tool, causing the contour of the workpiece surface to be inconsistent with expectations.
3. Repeatability: For workpieces that require continuous processing, thermal deformation may lead to accumulation of errors in each cutting, affecting the repeatability of the workpiece.
In order to reduce the impact of thermal deformation on accuracy, the following measures can be taken:
1. Optimize the structural design of the lathe to improve heat conduction efficiency and allow heat to dissipate faster.
2. Use high thermal conductivity materials, such as graphite and copper, to improve the thermal conductivity of lathe components.
3. Introduce a temperature control system to monitor the temperature of the lathe in real time and adjust it to keep the lathe at the optimal working temperature.
4. Use lubricants and coolants with high thermal stability to reduce the heat generated by friction.
5. Stop the machine in a timely manner during processing to allow the lathe to cool naturally and reduce the heat accumulation generated by continuous work.
6. Conduct regular training for operators to understand the principles and countermeasures of thermal deformation and improve their sensitivity to thermal deformation.
Thermal deformation is one of the key factors affecting the machining accuracy of CNC lathes. In order to ensure the accuracy and quality of processed workpieces, it is necessary to have an in-depth understanding of thermal deformation and take effective measures to control and reduce its impact. By optimizing lathe design, selecting high thermal conductivity materials, and introducing temperature control systems, the impact of thermal deformation on processing accuracy can be effectively reduced, and the processing performance and efficiency of CNC lathes can be further improved. At the same time, operator training and continuous attention to thermal deformation are also indispensable, helping to detect and solve potential problems in time to ensure smooth production.