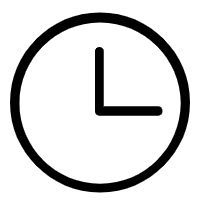
In the field of mechanical processing, CNC lathes, as an efficient and high-precision processing equipment, are widely used in the manufacturing of various parts. However, in the actual operation process, we sometimes encounter the problem of large size errors in the processed workpieces. This not only affects the quality of the product, but may also affect subsequent assembly and use. So, what is the cause of this problem?
First, we need to understand the basic working principle of CNC lathe. The CNC lathe mainly processes the workpiece by reading the preset processing program and controlling the movement trajectory and cutting parameters of the tool. Therefore, the accuracy of the machining program is directly related to the accuracy of the workpiece size. If the size parameters set in the program are incorrect, or there are logic errors in the program itself, the size of the processed workpiece may deviate.
Secondly, the influence of cutting tools and fixtures cannot be ignored. The wear of the tool, the shape of the tool tip, the installation position of the tool, the clamping force of the fixture and the positioning accuracy of the fixture will all affect the processing size of the workpiece. For example, severe tool wear or incorrect installation may cause uneven force during the cutting process, resulting in deviations in the size of the workpiece.
In addition, temperature changes and material properties during processing are also important influencing factors. Fluctuations in temperature may cause slight deformations of the tool or workpiece, and different materials have different thermal expansion coefficients and cutting characteristics, which may affect the size of the workpiece.
To sum up, the reasons for the large size error of workpieces processed by CNC lathes mainly include processing program errors, the influence of tools and fixtures, as well as the influence of factors such as temperature and material properties. In order to improve the accuracy of workpiece dimensions, we need to start from these aspects and strengthen measures such as program verification, regular inspection and replacement of tools, maintaining a constant temperature in the processing environment, and fully understanding the characteristics of the material. At the same time, for abnormal situations during the processing process, the causes should be discovered and analyzed in time, and corresponding corrective measures should be taken to ensure that the dimensional accuracy of the workpiece meets the requirements.