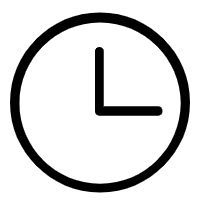
The machining center is a high-precision, high-efficiency machine tool that is widely used in aviation, automobiles, electronics, machinery and other industries. During the processing, wavy patterns sometimes appear, which affects product quality and processing effects. Let’s analyze the reasons for the formation of wave patterns.
1. The rigidity of the machine tool is insufficient. The machining center is not rigid enough and is prone to vibration during processing, resulting in wavy patterns. To solve this problem, methods such as strengthening the rigidity of the machine tool and adjusting cutting parameters can be used.
2. The tool is severely worn. Serious tool wear and poor cutting results will lead to wavy patterns on the machined surface. At this time, the tool should be replaced in time and the cutting parameters should be adjusted to meet the processing requirements.
3. The materials of the workpieces are different. Workpieces made of different materials will produce different deformations and quality problems during cutting, especially workpieces with different hardness, toughness, cutting temperature, etc., which will lead to wavy patterns on the machined surface. In this case, the cutting parameters and tool parameters should be adjusted reasonably, and different processing strategies should be adopted for different workpieces.
Therefore, to eliminate corrugation, some measures need to be taken to ensure processing quality and accuracy. First of all, the rigidity of the machine tool must be ensured. The quality and wear of the cutting tools are also very critical. The material of the workpiece must also be strictly selected and processed, so as to ensure that the processed workpiece achieves the ideal effect. During the machining process, the cutting parameters should always be adjusted according to the machining conditions, worn tools should be replaced in time, and a high degree of flatness of the workpiece surface should be maintained to achieve better processing results.