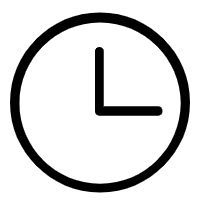
Knife collision is a common problem during CNC lathe processing, which may cause equipment damage, scrapped workpieces, and even operator injuries. There are many reasons for knife collisions. Here are some common causes and preventive measures:
1. Programming errors: When writing a processing program, if the workpiece coordinate system, tool parameters or processing parameters are not correctly set, it may cause the tool to collide with the workpiece or chuck during processing. To avoid this, programmers should carefully check all parameters and run simulations to check if there is a risk of collision.
2. Improper tool selection: Using unsuitable tools or improper tool lengths may lead to collisions during processing. Therefore, it is crucial to select the right tool and adjust the tool length to the workpiece.
3. The workpiece is not clamped firmly: If the workpiece is not clamped firmly on the chuck, it may cause vibration or displacement during processing, leading to a tool collision accident. Ensuring the workpiece is securely clamped on the chuck is key to preventing tool collisions.
4. Incorrect tool compensation settings: Incorrect tool compensation settings may cause the tool path to deviate from the actual position, causing collisions. Therefore, the tool compensation value should be carefully checked and corrected before processing.
5. Improper equipment maintenance: If the mechanical components of CNC lathes, such as guide rails, bearings, etc., are not maintained for a long time or are poorly lubricated, it may lead to a decrease in equipment accuracy and increase the risk of tool collision. Regular maintenance of equipment and keeping it in good operating condition is necessary.
6. Operator error: The operator is not fully trained or unfamiliar with the operation of the equipment, which may lead to misoperation and knife collision. Therefore, it is crucial to adequately train operators and ensure they are familiar with equipment operation.
To sum up, to avoid the tool collision problem during CNC lathe processing, comprehensive consideration and prevention need to be carried out from multiple aspects such as programming, tool selection, workpiece clamping, tool compensation settings, equipment maintenance and operator training.