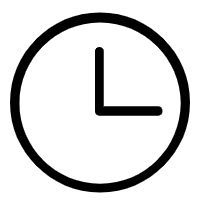
There are some significant differences in design and functionality between vertical lathes and regular lathes.
First of all, the spindle of a vertical lathe is vertical, which is equivalent to standing an ordinary lathe upright. This design makes vertical lathes particularly suitable for machining heavy parts with large diameters and short lengths. Since the workbench is in a horizontal position, operations such as clamping and correction of workpieces are more convenient. This layout also reduces the load on the spindle and bearings, so the vertical lathe can maintain working accuracy for a longer period of time.
Secondly, the vertical lathe has a wide range of processing. It can process internal and external cylinders, conical surfaces, end planes, grooves, chamfers, etc., while ordinary lathes are mainly used to process the internal and external rotating surfaces, end faces and various internal and external surfaces of the workpiece. thread.
In addition, the spindle of an ordinary lathe is placed in a horizontal manner, so it is often called a horizontal lathe. Its main components such as spindle box, feed box, slide box, tool rest, tailstock, feed rod, lead screw and bed are all designed and laid out around the spindle. This structure gives ordinary lathes advantages in processing various types of workpieces such as shafts, discs, rings, etc., and can perform various processes such as drilling, reaming, tapping and knurling.
In general, vertical lathes and ordinary lathes differ in spindle direction, processing range and application fields. Vertical lathes are more suitable for processing heavy parts with large diameters and short lengths, while ordinary lathes are better at processing multiple types of workpieces and can process a variety of processes.