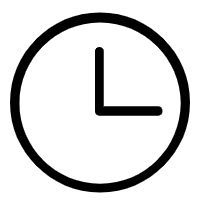
The occurrence of taper ellipse problems may be caused by a number of factors on the CNC lathe, including problems with the machine tool, tool, workpiece, or program. Here are some suggestions that may help you solve this problem:
1. Check the workpiece clamping: Make sure the workpiece clamping is stable and correct. Unstable clamping can cause the workpiece to shift during machining, causing tapers or ovals.
2. Check the cutting tools: The condition of the cutting tools is crucial to the processing quality. Make sure the knives are sharp and not damaged or worn. Use the right tool type and size and avoid tools that are severely worn.
3. Adjust cutting parameters: Check the cutting parameters in the CNC program, including cutting speed, feed speed and cutting depth. Adjusting these parameters may help improve processing quality.
4. Check the CNC program: Make sure the CNC program is correct. Wrong procedures can result in irregular cutting paths, causing tapers or ovals.
5. Calibrate machine tools: Regularly check and calibrate CNC machine tools, including the verticality and horizontality of the axis. Machine tool instability can result in uneven cuts, creating tapers or ovals.
6. Check the cooling system: Ensure that the cooling system is operating normally to prevent deformation caused by overheating. Proper cooling helps keep the workpiece and tool within the proper temperature range.
7. Check the workpiece material: The properties of the workpiece material may also affect the processing results. Make sure to select the workpiece material suitable for the machining and replace the material if necessary.
8. Adjust fixtures and tooling: Check the status of fixtures and tooling to ensure their stability and accuracy. Improper fixture settings can cause the workpiece to shift or deform.
9. Implement process optimization: Analyze the processing process, optimize process parameters, and may need to make some adjustments according to specific circumstances to obtain better processing results.
If the problem persists, more in-depth troubleshooting may be required, and sometimes it may be necessary to call in a professional CNC repairman for further inspection and adjustments. Make sure you use caution when making adjustments to your machine or program to avoid further problems.