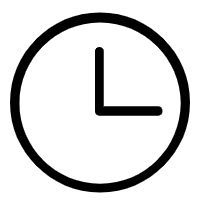
When CNC lathes process thin-walled parts, you need to pay attention to some special techniques and operating details to ensure processing quality and avoid deformation. Here are some tips for CNC lathe machining of thin-walled parts:
1. Reasonable selection of cutting tools: Choosing the right cutting tools for CNC lathes is crucial for processing thin-walled parts. Using high-quality tools, especially those with thin blades, can reduce cutting forces and reduce the possibility of thermal deformation.
2. Reduce the cutting speed: Reducing the cutting speed of the CNC lathe helps reduce the risk of thermal deformation. Appropriate cutting speed can reduce the cutting temperature, slow down the heat conduction speed, and reduce the impact on thin-walled structures.
3. Optimize the feed speed: Reasonably selecting and controlling the CNC lathe feed speed can reduce the cutting force and reduce the impact on thin-walled parts. Excessive feed rates may cause vibration and deformation.
4. Use coolant: Using appropriate coolant during CNC lathe processing can effectively reduce the cutting temperature, slow down the heat conduction speed, and help reduce deformation. At the same time, coolant can also reduce friction in the cutting zone.
5. Appropriate tool paths: Select appropriate CNC lathe tool paths and cutting methods to minimize the effects of vibration and cutting forces. Avoid overcutting or overcutting in thin-walled areas.
6. Support and clamping: When CNC lathes process thin-walled parts, ensure that the workpiece is fully supported and clamped. Special clamp designs may be considered to reduce the possibility of deformation.
7. Avoid excessive cutting depth: CNC lathes avoid cutting too deep at one time and can cut in batches to reduce cutting force and help reduce the risk of thermal deformation.
8. Appropriate cutting direction: Choosing the appropriate cutting direction for CNC lathes can help reduce the impact of cutting forces on thin-walled parts. Generally, cutting along thin walls reduces deformation.
9. Regular measurement and inspection: CNC lathes regularly measure and inspect the dimensions of parts during processing and whether there are signs of deformation. Adjust processing parameters in a timely manner to ensure the accuracy and quality of parts.
10. Reasonable tool unloading: After cutting, CNC lathes should pay attention to gradually unloading the tool to avoid vibration and deformation caused by sudden tool withdrawal.
By comprehensively applying the above techniques, the risk of deformation when processing thin-walled parts with CNC lathes can be effectively reduced, and the processing quality and accuracy can be improved.