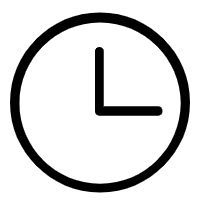
There are various reasons for CNC vertical lathe collisions, mainly including the following aspects:
1. Program writing errors: Wrong CNC vertical lathe process arrangements, poor consideration of process undertaking relationships, and wrong parameter settings may lead to machine crashes. For example, the coordinates are set so that the bottom is zero, but in reality the top is 0; the safety height is too low, causing the tool to be unable to completely lift out the workpiece; problems may also arise if program path analysis and inspection are not rigorous.
2. Program sheet remark error: When setting and changing the CNC vertical lathe program sheet, the principle of replacing the old with the new should be followed. If the old program sheet is not destroyed, the new and old programs are mixed and used, which may lead to a machine crash.
3. Tool measurement errors: Incorrect input of diameter and length of CNC vertical lathe tools, input errors of workpiece dimensions and other related geometric dimensions, and positioning errors of the initial position of the workpiece may cause machine collisions.
4. The blank exceeds expectations: The blank of the CNC vertical lathe is too large and does not match the blank set by the program, which is also a reason for the collision.
5. Improper operation: When the CNC vertical hand wheel is used to set the tool, due to unskilled operation, collisions between the tool and the workpiece often occur. In addition, when setting the tool, use the hand wheel to quickly bring the tool close to the workpiece. If the feed speed is set too high, it may also cause the tool to collide with the workpiece.
6. Missing auxiliary function instructions: When the CNC vertical lathe program is interrupted, if the auxiliary function instructions are not called again, abnormal program preparation may cause a collision.
7. Tool changing error: When a CNC vertical lathe is manually temporarily changing tools, if a short tool is replaced with a long tool or a small tool is replaced with a large tool, tool collision may also occur.
8. CNC system problems: When the CNC lathe uses decimal point programming, if the operator is careless or confuses the concept, and writes the decimal point programming incorrectly or does not meet the requirements, it may cause a car crash. In addition, faults in the CNC system or machine tools may also cause collisions.
In order to avoid CNC vertical lathe collisions, operators should strictly follow the procedures, carefully check and test the program, ensure that the parameters are set correctly, and perform regular maintenance on the machine tool. At the same time, risk factors that may cause a collision should be identified in advance and corresponding measures should be taken to prevent them.