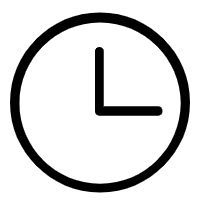
CNC lathe is a high-precision, high-efficiency automated mechanical equipment that is widely used in industrial production. In the production process of CNC lathes, input and output electrical components are important components. Their role is to convert human-designed data into instructions that machines can understand and execute. So, what are the commonly used input and output electrical components of CNC lathes?
Enter electrical components:
1. Programming equipment: Programming equipment is one of the most basic input electrical components in CNC lathes. It usually uses a CAD/CAM system for advanced programming or simple text programming software for basic programming.
2. Position sensor: The position sensor is one of the key equipment of CNC lathe. It controls the machining process by determining tool position and workbench position. Position sensor signals can be used to calculate the size and shape of the workpiece in preparation for further processing.
3. Speed sensor: The speed sensor is an input electrical component that measures the rotational speed of a tool or workbench during processing. They help control the speed and direction of the machining process to avoid dangerous situations.
4. Force sensor: Force sensor is used to detect the force exerted on the surface of the tool or workbench. Regularly monitoring force sensor data can help operators determine if cutting conditions are appropriate.
5. Temperature sensor: The temperature sensor is used to sense the temperature of the surrounding environment. Temperature changes have an important impact on the processing process of CNC lathes, so the signal of the temperature sensor is also very important.
Output electrical components:
1. Servo controller: Servo controller is one of the most common output electrical components in CNC lathes. It controls the movement of a tool or workbench and compensates for position errors.
2. Motor driver: Motor driver is used to convert control signals to generate movement of the workbench or tool. Factors such as motor driver parameters and working conditions have a direct impact on the accuracy and speed of the machining process.
3. Hydraulic controller: Hydraulic controllers use hydraulic systems to transport and control fluids. It is mainly used to control tool and cutter conversion operations.
4. Photoelectric switch: Photoelectric switch is usually used to detect the position of the workpiece in the processing area and guide the movement direction of the machine during processing.
In general, input and output electrical components are one of the keys to the operation of CNC lathes. They convert the instructions that the machine needs to execute into a computer-readable form, thereby automating production and improving efficiency and accuracy. In practical applications, operators need to promptly adjust the parameters of tools and worktables based on the signals fed back by the data collector and controller to ensure that the CNC lathe can process with the expected accuracy, speed and quality.