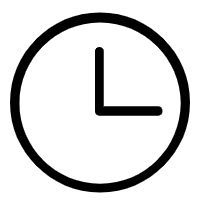
In high-precision CNC lathe processing, correct clamping is crucial to ensure turning accuracy. The following are some commonly used clamping methods and precautions:
1. Select the appropriate fixture: The CNC lathe selects the appropriate fixture according to the shape, size and processing requirements of the workpiece. Commonly used CNC lathe fixtures include three-jaw chucks, four-jaw chucks, spring clamps, vacuum adsorption clamps, etc.
2. Ensure the rigidity of the fixture: The rigidity of the CNC lathe fixture directly affects the processing accuracy. Ensure that the CNC lathe fixture has sufficient rigidity to firmly clamp the workpiece and avoid vibration and deformation during the processing.
3. Clamp the workpiece correctly: The CNC lathe adopts appropriate clamping methods according to the characteristics and processing requirements of the workpiece to ensure that the CNC lathe workpiece is clamped firmly and stably without movement or deformation. For thin-walled workpieces, multi-point clamping or support pads can be used to reduce deformation.
4. Centering adjustment: Before clamping the workpiece, the CNC lathe performs precise centering adjustments on the workpiece and fixture to ensure that the CNC lathe workpiece axis is consistent with the machine tool spindle axis to avoid processing errors caused by eccentricity.
5. Pre-tightening force control: Control the pre-tightening force of the fixture to ensure that the CNC lathe fixture holds the workpiece with a moderate force, which must not only ensure firmness but also avoid excessive deformation.
6. Verification before and after processing: Before and after the CNC lathe is processed, the CNC lathe measures the size and geometry of the workpiece to verify the processing accuracy, and promptly discovers and adjusts possible problems in the processing.
7. Regular inspection and maintenance: CNC lathes should regularly check the wear and tear of the fixtures, promptly replace damaged or severely worn fixture parts, and keep the CNC lathe fixtures in good condition.
8. Reasonably arrange the tool path: When programming a CNC lathe, reasonably arrange the CNC lathe tool path and cutting parameters to reduce the impact of cutting forces on the workpiece and fixture, and improve processing accuracy and surface quality.
Through the above CNC lathe clamping methods and precautions, CNC lathes can effectively ensure the turning accuracy of high-precision CNC lathe processing and improve processing quality and efficiency.