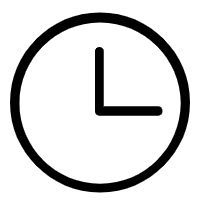
For CNC vertical lathes, clamping workpieces is a very important link. Because a good workpiece clamping method can improve processing efficiency, ensure processing quality, and extend the service life of machine tools. So how does the CNC vertical lathe clamp the workpiece?
First of all, workpiece clamping needs to take into account factors such as the different shapes, sizes, and processing content of the workpiece. Therefore, when formulating a clamping plan, evaluation and selection should be made based on the actual situation, and appropriate fixtures and fixture accessories should be selected to meet the different processing needs of the workpiece.
Secondly, when clamping the workpiece, the clamping force and clamping method need to be reasonably selected. Some small-sized workpieces can be directly clamped with aluminum alloy clamps; while for large workpieces, efficient pneumatic clamps, quick-change clamping equipment and other technical means can be considered to improve clamping force and work efficiency. Of course, the choice of fixture also needs to take into account factors such as the processing location of the workpiece, processing accuracy, and frequency of work.
Finally, attention needs to be paid to the maintenance and management of fixtures. Some efficient clamping equipment, its instrument dials and sensors require regular maintenance to ensure the stability of clamping force and position accuracy. At the same time, you should also pay attention to regular cleaning and maintenance during daily use to prevent the board from rusting, deformation, or mechanical component failure.
In short, how to clamp workpieces on a CNC vertical lathe requires detailed analysis based on factors such as processing content, workpiece shape, and fixture type. Only by rationally selecting fixtures and fixture accessories and standardizing the use and maintenance of fixtures can machine tool processing efficiency be improved, processing quality guaranteed, and greater benefits provided for industrial production.