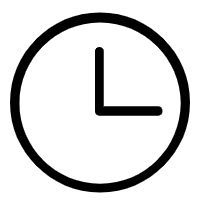
Reverse error refers to an error caused by the gap or lag in the transmission system when the machine tool changes the direction of motion. In precision CNC lathes, reverse error may have a negative impact on machining accuracy and surface quality. The specific manifestations are as follows:
1. Reduced machining accuracy: The reverse error will cause the tool to have a certain pause or lag when changing the cutting direction, causing the cutting trajectory on the workpiece to deviate, thus reducing the machining accuracy. Especially when fine contouring or high-precision machining is required, reverse error can become a serious problem.
2. Decrease in surface quality: Reverse error will cause discontinuity in the processing trajectory, which may leave obvious marks or flaws on the surface of the workpiece, affecting the surface quality. Especially for workpieces that require a higher surface finish, the reverse error may lead to an increase in surface roughness.
3. Increased dimensional deviation: Reverse error will cause additional movement of the tool when the cutting direction is changed, resulting in deviations in the processing dimensions. This may cause the size of the machined part to be inconsistent with the design requirements, affecting its function and assembly.
4. Reduced processing efficiency: In order to avoid the impact of reverse error on processing accuracy and surface quality, operators may adopt conservative processing strategies such as reducing the feed speed or increasing the cutting allowance, which will lead to a reduction in processing efficiency.
In order to reduce the impact of reverse error on precision CNC lathes, the following measures can be taken:
1. Transmission system optimization: Optimizing the transmission system, reducing the gaps between transmission parts, and using more precise transmission devices can reduce the incidence of reverse errors.
2. Reverse compensation: Set the reverse compensation function in the CNC system to automatically adjust the movement trajectory when the movement direction changes to offset the impact of reverse error on machining accuracy.
3. Regular maintenance: Carry out regular maintenance on CNC lathes, check the wear and tear of components such as the transmission system and guide rails, and make timely adjustments or replacements to ensure the movement accuracy and stability of the machine tool.
4. Finely adjust parameters: During the processing process, according to the requirements of the specific workpiece and processing conditions, finely adjust the parameters of the CNC system to minimize the impact of reverse errors.
Through the comprehensive application of the above measures, the impact of reverse error on the processing quality of precision CNC lathes can be effectively reduced, the processing accuracy and efficiency can be improved, and the quality and dimensional accuracy of the processed parts can be ensured.