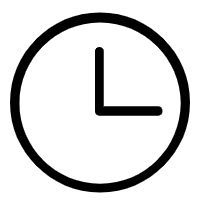
In CNC lathe workpiece processing, specification errors may be caused by many reasons. These reasons involve many aspects such as CNC systems, tools, workpieces, and machine tools. Here are some of the main causes of specification errors:
1. CNC program errors: There may be syntax errors, logic errors or coordinate system setting errors when writing CNC programs for CNC lathes. These errors will lead to deviations in the workpiece processing position, thus causing specification errors.
2. Tool deviation: During the use of CNC lathe tools, tool deviation may occur due to wear or damage. If the CNC system does not provide timely tool correction and compensation, it is easy to cause specification errors.
3. Tool path planning errors: If the CNC system makes errors in tool path planning, such as trajectories that intersect or are not smooth, it may cause irregularities in the workpiece surface or incorrect shape.
4. Machine tool errors: Errors in CNC lathes, including servo system errors, guide rail errors, etc., may lead to deviations in the processing position of the workpiece, thereby causing specification errors.
5. Workpiece fixation problems: Problems such as weak fixation of CNC lathe workpieces, unreasonable fixture design or damaged fixtures may cause the workpiece to move during the processing, thereby causing specification errors.
6. Wrong setting of cutting parameters: If the cutting speed, feed speed and other parameters of the CNC lathe are not set properly, it may lead to poor cutting quality and cause specification errors.
7. Material changes: Changes in the material properties of CNC lathes, such as changes in material dimensions caused by temperature changes, may cause specification errors.
8. Measurement error: The measurement tools used by CNC lathes may have errors. If the measurement is inaccurate, it can easily lead to specification errors.
9. Operator errors: CNC lathe operators are not skilled in the operation of CNC lathes, and misoperation may lead to specification errors.
10. Power supply problems: Unstable power supply or electrical problems in CNC lathes may lead to instability of the CNC system, thereby causing specification errors.
In order to reduce specification errors, manufacturers usually adopt strict quality control measures, including regular machine tool maintenance, tool calibration, review and testing of CNC programs, etc. Additionally, training operators to ensure they are familiar with correct operating procedures is critical. Regular inspection and calibration of equipment, as well as the use of high-quality tools and cutting tools, are important factors in maintaining the quality of workpiece processing.